Understanding Thin-Film Technology
Thin-film technology involves depositing skinny layers of material (usually from a few nanometers to a few micrometers thick) onto a substrate. These layers can be made of metals, semiconductors, insulators, or other materials, and are used to create functional electronic components. This technology is particularly important in manufacturing electronic devices as it enables high precision and performance of components. Thin-film deposition is typically done through physical vapor deposition (PVD) or chemical vapor deposition (CVD), ensuring the quality and performance of the final product.
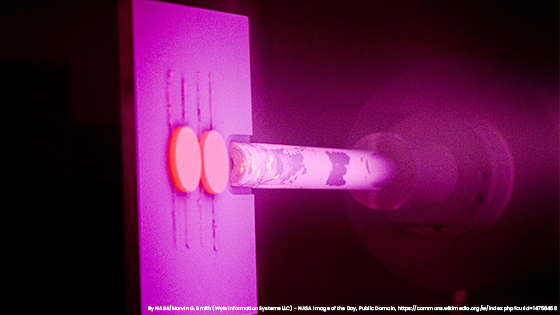
The development of thin-film technology dates back to the mid-20th century when significant advances were made in material science and vacuum deposition techniques. Initially, thin-film technology was mainly applied in the semiconductor industry for the manufacture of transistors and integrated circuits. As technology advanced and demand increased, the application range of thin-film technology rapidly expanded. Today, it is widely used in sensor manufacturing, optical coatings, solar cells, hard disk drives, and anti-corrosion coatings, among others. For example, in sensor manufacturing, thin-film technology is used to produce pressure sensors, gas sensors, and temperature sensors, which are characterized by high sensitivity and precision. Additionally, the application of thin-film technology in microelectromechanical systems (MEMS) and nanotechnology is also growing, providing important support for innovation and development in these fields.
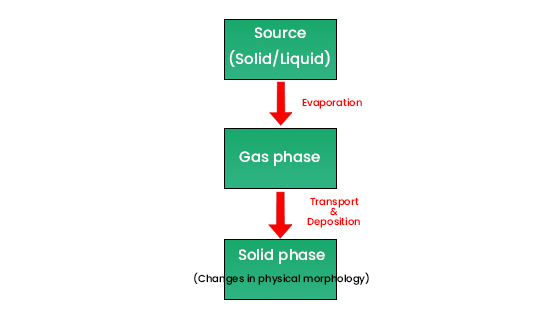
Key features of thin-film technology include its high precision, flexibility, and multi-function integration capability. High precision allows thin-film technology to achieve extremely accurate measurements within a small size range, which is crucial for devices like pressure sensors that need to maintain accurate pressure measurements under various environmental conditions. The flexibility of thin films allows them to adapt to various substrates and application needs, enabling deposition on different substrates such as silicon, glass, metals, and plastics, thereby achieving multiple functions. Moreover, thin-film technology can be integrated with other technologies and materials to create composite devices with multiple functions. For instance, combining thin-film technology with MEMS can produce miniature pressure sensors that are not only small and lightweight but also highly sensitive and reliable.
Thin-film technology also can integrate multiple functions into a single device, meaning that sensing, measurement, and data processing can be achieved simultaneously within a thin-film layer, simplifying the design and manufacturing process of the device. This integration capability not only enhances device performance and reliability but also reduces manufacturing costs and complexity. In the development of pressure sensors, thin-film technology can significantly improve sensor performance, allowing them to work stably in various complex environments.
Integration of Thin-Film Technology in Pressure Sensors
The integration of thin-film technology in pressure sensors aims to enhance performance, reduce size, and increase sensitivity. By precisely controlling material properties and layer thickness, thin-film technology makes the development of high-precision sensors possible. This integration not only improves the overall performance of the sensors but also brings significant advantages in several key aspects.
Firstly, thin-film technology enables the miniaturization of sensors. Traditional pressure sensors often face limitations in size and weight, while thin-film technology allows for the manufacture of smaller, lighter sensors without compromising performance. This is particularly important for applications with limited space or requiring lightweight solutions, such as medical devices and MEMS.
Secondly, thin-film sensors excel in enhancing sensitivity. Thin-film technology can detect minute pressure changes with high precision, making these sensors advantageous in environments requiring accurate measurements. For example, in industrial automation and environmental monitoring, thin-film pressure sensors can provide precise data, thereby improving overall system efficiency and reliability.
Moreover, thin-film technology improves the reliability and durability of pressure sensors. The high uniformity and stability of thin-film layers ensure consistent performance over long-term use. Compared to traditional sensors, thin-film sensors can maintain good performance even under extreme environmental conditions, making them widely applicable in fields such as aerospace and automotive industries.
Compared to traditional methods, thin-film technology offers a lightweight, compact, and highly sensitive alternative. Traditional pressure sensors often face challenges in size, weight, and precision, while thin-film technology, with its superior material properties and manufacturing processes, overcomes these limitations. Thin-film sensors not only have advantages in size and weight but also significantly outperform traditional sensors in terms of precision and sensitivity. These advantages make thin-film technology an important part of the development of modern sensor technology.
Materials for Thin-Film Pressure Sensors
The choice of materials for thin-film pressure sensors is crucial as these materials directly impact the performance and reliability of the sensors.
Common Materials
Common materials used in thin-film pressure sensors include metals like gold, platinum, and aluminum, known for their excellent conductivity and corrosion resistance. Gold, as a highly conductive material, is often used in the electrode parts of sensors to ensure the accuracy and stability of signal transmission. Platinum, due to its excellent thermal stability and oxidation resistance, is widely used in sensors for high-temperature environments. Aluminum, being lightweight and having good conductivity, is commonly used in sensor applications requiring weight control. Additionally, semiconductor materials such as silicon and germanium are widely used in thin-film pressure sensors due to their good mechanical properties and sensitivity, playing an indispensable role in MEMS.
Advanced Materials
With technological development, advanced materials such as nanocomposites and graphene are gaining increasing attention for their application in thin-film pressure sensors. These materials are widely researched for their excellent properties and potential to further enhance sensor performance. Nanocomposites combine the advantages of different materials, offering superior mechanical strength and conductivity, which can significantly improve sensor sensitivity and durability. Graphene, with its single-atom layer structure and outstanding electrical properties, is considered an ideal choice for future sensor materials. It not only has ultra-high conductivity but also exhibits excellent mechanical strength and elasticity, showing great potential in the development of ultra-sensitive pressure sensors.
Material Properties
The selection of materials for thin-film pressure sensors is based on their electrical, mechanical, and thermal properties to ensure optimal performance under various operating conditions. For example, sensors used in high-temperature environments require materials with excellent thermal stability and oxidation resistance, while applications requiring high sensitivity consider the electrical conductivity and mechanical elasticity modulus of the materials. By comprehensively considering these material properties, designers can choose the most suitable materials for specific application needs, ensuring the reliability and accuracy of sensors in various complex environments.
Design Considerations for Thin-Film Pressure Sensors
Design considerations for thin-film pressure sensors aim to ensure their performance, reliability, and stability in various applications.
Structural Design
The structural design of thin-film pressure sensors must ensure mechanical stability and robustness while maintaining sensitivity and accuracy. This requires designers to consider not only the physical properties of the thin film but also the mechanical load and environmental pressure in actual applications. The sensor's structural design should withstand various mechanical stresses and environmental changes while maintaining a stable output signal.
Sensitivity
Sensitivity is a key factor in the design of pressure sensors, influenced by material selection, thin-film thickness, and manufacturing technology. High-sensitivity sensors can detect minute pressure changes, crucial for precision measurement and control applications. Material selection directly impacts sensor sensitivity; different materials have varying mechanical and electrical properties, suitable for different application needs. Thin-film thickness is also a critical factor; the thinner the film, the higher the sensitivity, but this might reduce mechanical strength, necessitating a balance between sensitivity and strength.
Accuracy and Precision
Achieving high accuracy and precision in thin-film pressure sensors requires careful design and manufacturing processes to ensure measurement reliability and repeatability. This includes precisely controlling the thickness and uniformity of the thin film, selecting suitable substrates, and optimizing manufacturing processes. Any minor deviation in the manufacturing process can affect sensor performance, making strict quality control and testing necessary.
Performance Characteristics Response Time
Thin-film pressure sensors typically have a fast response time, crucial for dynamic applications requiring real-time pressure monitoring. A fast response time ensures that the sensor can promptly capture pressure changes, providing real-time data support for applications in fields like industrial automation, medical devices, and aerospace.
Durability
Selecting appropriate materials and adopting reliable manufacturing techniques enhance the durability of thin-film pressure sensors, ensuring long-term reliability. Durability is crucial for the long-term stable operation of sensors, especially those working in harsh environmental conditions, such as high temperatures, high humidity, or corrosive environments.
Environmental Stability
Thin-film pressure sensors must maintain consistent performance under various environmental conditions, including temperature fluctuations, humidity, and mechanical stress. This requires sensors to have good environmental stability, be capable of operating within a wide temperature range, and be insensitive to changes in humidity and mechanical stress. Material selection and packaging design play a key role in ensuring the environmental stability of sensors.
Applications of Thin-Film Pressure Sensors
In the automotive industry, thin-film pressure sensors are used in tire pressure monitoring systems (TPMS) to provide real-time tire pressure data, enhancing safety and performance. In engine management systems, these sensors monitor fuel and air pressure, ensuring optimal engine performance and efficiency. Additionally, automotive safety systems like airbags and braking systems rely on thin-film pressure sensors for precise pressure measurement and timely activation.
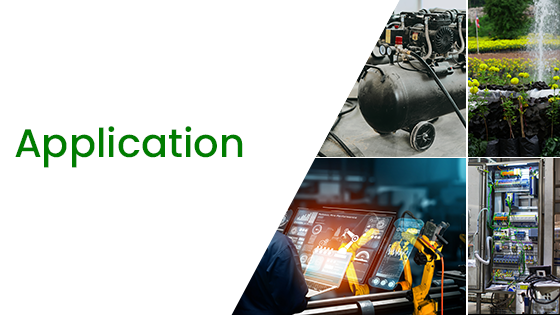
In the medical field, thin-film pressure sensors are used in blood pressure monitors, providing accurate and non-invasive measurements essential for patient care and diagnosis. They are also used in implantable sensors for continuous physiological monitoring, improving patient treatment outcomes. Wearable medical devices, such as fitness trackers and health monitors, use these sensors to track vital signs and physical activities.
In the aerospace sector, thin-film pressure sensors are used for cabin pressure monitoring, ensuring optimal cabin pressure for passenger comfort and safety. They are also used for structural health monitoring, capable of detecting potential issues before they become severe. Moreover, these sensors are critical in spacecraft environmental control systems, ensuring stable conditions for crew and equipment.
In industrial applications, thin-film pressure sensors are used for precise process control, ensuring optimal operation and efficiency. Robotic systems rely on these sensors for tactile feedback and pressure sensing, enhancing their performance and capabilities. Industrial safety systems also use thin-film pressure sensors to detect and respond to pressure changes, preventing accidents and ensuring worker safety.
Frequently Asked Questions
What are the main advantages of thin-film pressure sensors?
Thin-film pressure sensors offer high sensitivity, miniaturization, and enhanced reliability, making them ideal for various applications. Their high sensitivity allows them to detect minute pressure changes, the miniaturized design makes them suitable for space-constrained applications, and enhanced reliability ensures long-term stable operation in harsh environments.
How do thin-film pressure sensors differ from traditional sensors?
Thin-film pressure sensors are more precise, compact, and generally more durable than traditional bulk sensors. They offer better performance in demanding applications, are capable of operating within a broader range of temperatures and pressures, and possess higher sensitivity and response speed. These characteristics make thin-film sensors excel in many high-demand applications.
What materials are commonly used in thin-film pressure sensors?
Common materials include metals like gold and platinum, semiconductors like silicon, and advanced materials like graphene. Gold and platinum are widely used for their excellent conductivity and corrosion resistance in the sensor electrodes. Silicon is commonly used in semiconductor thin films due to its good mechanical properties and electronic characteristics, while graphene is considered an ideal choice for future sensor materials due to its outstanding electrical properties and mechanical strength.
Which industries benefit most from thin-film pressure sensors?
Automotive, medical, aerospace, consumer electronics, and industrial automation industries significantly benefit from thin-film pressure sensors. In the automotive industry, these sensors are used for tire pressure monitoring and engine management; in the medical field, they are used for blood pressure monitoring and implantable sensors; in the aerospace sector, they are used for cabin pressure monitoring and structural health monitoring; in consumer electronics, they enhance the user experience of smart devices; and in industrial automation, they are used for process control and robotics.
What manufacturing techniques are used for thin-film pressure sensors?
Common techniques include sputtering, chemical vapor deposition (CVD), physical vapor deposition (PVD), and atomic layer deposition (ALD). These techniques can precisely control the thickness, uniformity, and composition of the thin film, ensuring sensor performance and reliability. Sputtering is a widely used physical vapor deposition method for producing metal thin films; CVD and PVD techniques are commonly used for depositing semiconductors and insulating materials; ALD can control the thickness of thin films at the atomic level, suitable for preparing ultra-thin films.
References:
1. Ohring, M. (2001). "Materials Science of Thin Films." Academic Press.
Post time: Jun-28-2024