Introduction
As a procurement or technical personnel, do you often feel conflicted when choosing a pressure sensor ? With a wide array of models and products on the market, selecting the most suitable one is indeed a considerable challenge. Each project and application has its unique requirements, and different types of pressure sensors have their own advantages and disadvantages. You might wonder: which type of pressure sensor is best suited to my needs? An inappropriate choice can lead to inaccurate measurements, additional maintenance costs, and even affect the normal operation of the entire system. Therefore, understanding the basic classification and application scenarios of different types of pressure sensors becomes key to making an informed choice. This article will provide a detailed introduction to pressure sensors classified by measurement reference, hoping to offer some references and assistance for your selection, so you no longer hesitate when facing numerous options.
Pressure sensors are devices used to measure the pressure of gases or liquids and are widely used in various industries, including medical, aerospace, environmental monitoring, and more. By converting physical pressure into electrical signals, pressure sensors enable the monitoring, control, and data recording of pressure values. Based on different measurement principles and technologies, pressure sensors can be divided into various types to meet the needs of various application scenarios.
Choosing the right pressure sensor is crucial for ensuring the reliability, accuracy, and efficiency of the system. Different application scenarios have different requirements for pressure sensors. For example, in industrial automation, high-precision, and stable pressure sensors are needed, while in medical devices, small-size and high-sensitivity sensors are required. Therefore, understanding the classification and applicable scenarios of pressure sensors can help engineers and technical personnel make more informed choices, ensuring that the selected sensors meet the specific needs of the application, thereby improving the overall system performance and reliability.
Pressure Sensors Classified by Measurement Reference
Absolute Pressure Sensors
Absolute pressure sensors measure pressure relative to a vacuum and are suitable for applications requiring precise absolute pressure readings. These sensors work by sensing the difference between the vacuum and the measured pressure. Specifically, absolute pressure sensors typically have a sealed vacuum reference chamber. When external pressure is applied to the sensor's sensing element, it deforms, causing a change in the electrical signal. Because their reference is an absolute vacuum, absolute pressure sensors can provide highly accurate and stable pressure readings. They are widely used in meteorology, aerospace, and vacuum equipment. For example, in weather stations, absolute pressure sensors measure atmospheric pressure to help predict weather changes. In aerospace, they measure altitude and monitor pressure changes inside and outside aircraft. Despite their high measurement accuracy, absolute pressure sensors are relatively expensive and complex to install and maintain.
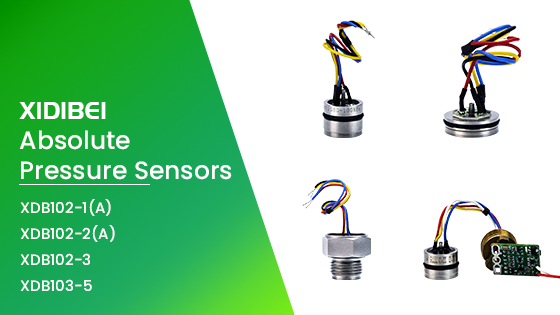
The absolute pressure sensor models we offer include XDB102-1(A), XDB102-2(A), XDB102-3, XDB103-5, and more.
Gauge Pressure Sensors
Gauge pressure sensors measure pressure relative to ambient atmospheric pressure and are the most common type of pressure sensor in industrial process control and daily applications. They work by sensing the difference between atmospheric pressure and the measured pressure. When the measured pressure is applied to the sensor's sensing element, it deforms, leading to changes in resistance, capacitance, or voltage, outputting an electrical signal proportional to the pressure. Gauge pressure sensors are widely used and cost-effective, suitable for various industrial and commercial applications such as level measurement, HVAC systems, and hydraulic systems. For instance, in level measurement, gauge pressure sensors can be installed at the bottom of storage tanks to calculate liquid levels by measuring the static pressure produced by the liquid. In HVAC systems, they monitor air pressure in ducts to ensure normal operation. However, their measurements can be affected by changes in atmospheric pressure, requiring frequent calibration in regions with significant atmospheric pressure variations to ensure accuracy.
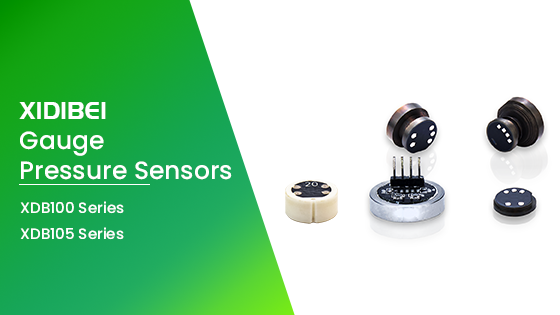
The relative pressure sensor models we offer include the XDB100 series , XDB105 series , and more.
Differential Pressure Sensors
Differential pressure sensors measure the pressure difference between two points and are essential tools for monitoring and controlling pressure changes in systems. They work by sensing the pressure difference between two measurement points. Differential pressure sensors usually have two pressure ports. When different pressures are applied to the sensor's sensing element, it deforms, causing a change in the electrical signal. These sensors are widely used in filter monitoring, flow measurement, and level measurement. For example, in filter monitoring, differential pressure sensors measure the pressure difference across the filter to determine the blockage level. In flow measurement, they calculate flow rates by measuring the pressure difference before and after fluid flow in pipes. In level measurement, they determine liquid levels by measuring the pressure difference between the top and bottom of storage tanks. While differential pressure sensors provide precise differential pressure measurements and reliable results, their installation and calibration are more complex, requiring good sealing between two measurement points to avoid measurement errors. They also need periodic maintenance and calibration to ensure measurement accuracy and long-term stability.
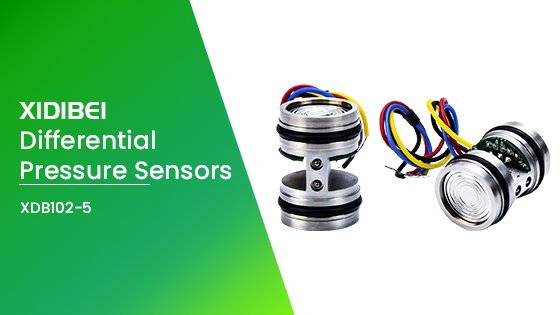
Key Factors in Choosing Pressure Sensors Classified by Measurement Reference
Selecting the right pressure sensor requires considering multiple factors to ensure accurate, reliable, and stable measurement results in specific applications. Here are the key factors to consider when choosing pressure sensors classified by measurement reference:
Application Need
First, clarifying the specific application scenario's requirements is the primary step in choosing a pressure sensor. Different application scenarios have different requirements for pressure sensors. For example, in meteorology, absolute pressure sensors are needed to measure atmospheric pressure; in industrial process control, gauge pressure sensors are widely used for monitoring and controlling system pressure; and in inflow and filter monitoring, differential pressure sensors are needed to measure the pressure difference between two points. Therefore, choosing the right type of pressure sensor based on specific application needs ensures optimal sensor performance in the application.
Measurement Accuracy
Measurement accuracy is a crucial factor when selecting pressure sensors. Different applications require different levels of pressure measurement accuracy. For example, medical devices and scientific research need high-accuracy pressure sensors, while some industrial applications may have lower accuracy requirements. When choosing pressure sensors, select the appropriate model and accuracy level based on the application's accuracy needs to ensure measurement results' accuracy and reliability.
Environmental Conditions
The working environment significantly impacts the performance of pressure sensors. When selecting pressure sensors, consider factors such as temperature, humidity, corrosion, and vibration in the working environment. For instance, in high or low-temperature environments, choose pressure sensors with good temperature compensation performance; in humid or corrosive environments, choose sensors with corrosion-resistant and waterproof housing. Additionally, in environments with strong vibrations, choose pressure sensors with excellent vibration resistance.
Response Time
Response time refers to the speed at which a pressure sensor responds to pressure changes. In some applications, fast response is critical, such as in automotive crash tests and dynamic pressure monitoring, where pressure sensors with extremely fast response times are needed to capture instantaneous pressure changes. Therefore, when choosing pressure sensors, select the appropriate model based on the application's response time requirements to ensure real-time monitoring and recording of pressure changes.
Stability and Repeatability
Stability and repeatability are important indicators of a pressure sensor's long-term performance. Stability refers to the sensor's ability to maintain consistent performance over time, while repeatability refers to the consistency of results in repeated measurements under the same conditions. In many applications, especially industrial automation, and scientific research, pressure sensors need to provide stable and consistent measurement results over time. Therefore, when choosing pressure sensors, prioritize models with high stability and repeatability to ensure long-term reliability.
Cost
Finally, cost is an unavoidable factor when selecting pressure sensors. Under the premise of meeting technical requirements, choose cost-effective sensors to control costs effectively. While high-performance pressure sensors are usually more expensive, selecting suitable mid-range performance sensors can also meet needs in some applications, maximizing cost-effectiveness. Therefore, consider both technical performance and cost when choosing pressure sensors to find the most suitable model.
By comprehensively considering these factors, engineers and technical personnel can make informed decisions when selecting pressure sensors, ensuring the chosen sensors meet specific application needs and provide long-term stable and reliable measurement results.
Common Application Scenarios Analysis
Absolute Pressure Sensors in Meteorology
In meteorology, absolute pressure sensors play a crucial role. They measure absolute atmospheric pressure relative to a vacuum, which is essential for weather forecasting and climate research. Weather stations typically install absolute pressure sensors to measure and record atmospheric pressure changes. These data can predict weather changes, such as high-pressure systems usually being associated with clear weather, while low-pressure systems may indicate storms or other severe weather. Additionally, absolute pressure sensors are widely used in high-altitude balloons and satellites to measure atmospheric pressure at different altitudes, helping scientists understand the structure and changes of the atmosphere. The advantages of absolute pressure sensors include high measurement accuracy and long-term stability, providing reliable data to support meteorological research and weather forecasting.
Gauge Pressure Sensors in Industrial Process Control
In industrial process control, gauge pressure sensors are indispensable tools. They measure pressure relative to ambient atmospheric pressure, helping monitor and control system pressure. They are widely used in various industrial fields, such as chemical, petroleum, natural gas, and manufacturing. For example, in chemical production, gauge pressure sensors monitor the pressure in reactors and pipelines, ensuring the process operates within a safe and effective pressure range. In level measurement applications, they can calculate liquid levels by measuring the pressure at the bottom of storage tanks. Additionally, gauge pressure sensors are crucial in HVAC systems, monitoring and regulating air pressure in ducts to ensure efficient operation. Their main advantages are wide application, low cost, and ease of installation and maintenance, meeting the needs of various industrial applications.
Differential Pressure Sensors in Filter Monitoring
Differential pressure sensors are extensively used in filter monitoring, providing real-time monitoring of the pressure difference across filters to determine their operational status and blockage level. In various industrial and environmental monitoring systems, they help ensure the normal operation of filtration systems. For instance, in HVAC systems, differential pressure sensors monitor air filter blockage. When the pressure difference exceeds a set value, the system alerts the need for filter replacement or cleaning. In water treatment systems, they monitor the pressure difference in water filters to ensure water quality and flow stability. Moreover, differential pressure sensors are widely used in the oil and gas industry to monitor pressure differences in pipelines and equipment, ensuring safe and efficient operations. Their advantages include precise differential pressure measurement and reliable results, although their installation and calibration are more complex, requiring professional operation.
Conclusion
Choosing the right pressure sensor is crucial for ensuring the reliability, accuracy, and efficiency of various systems. Whether it is absolute pressure sensors, gauge pressure sensors, or differential pressure sensors, their unique features and advantages make them suitable for specific application scenarios. By understanding the basic classification and application scenarios of pressure sensors, engineers and technical personnel can make informed choices based on specific needs, ensuring that the selected sensors meet the application's technical requirements and environmental conditions. Additionally, choosing the right pressure sensor requires considering measurement accuracy, environmental conditions, response time, stability, repeatability, and cost. In summary, understanding the working principles and application scenarios of different types of pressure sensors helps improve overall system performance and reliability, promoting technological progress and innovation.
Post time: Jul-09-2024