Introduction
In the previous article, we detailed the classification of pressure sensors by measurement reference, including absolute pressure sensors, gauge pressure sensors, and differential pressure sensors. We explored their working principles, application scenarios, and key selection factors, laying the foundation for choosing the right pressure sensor. If you haven't read the previous part, you can click here to read it. However, besides measurement reference, pressure sensors can also be classified by technology. Understanding different types of pressure sensors by technology can help us find the most suitable and high-performing sensor for specific applications.
Choosing pressure sensors by technology is crucial because different technologies have significant differences in measurement principles, accuracy, response time, temperature stability, and more. Whether in industrial automation, medical devices, aerospace, or environmental monitoring, selecting the appropriate type of pressure sensor can greatly enhance the reliability and efficiency of the system. Therefore, this article will delve into the working principles, application scenarios, and advantages and disadvantages of piezoresistive, capacitive, piezoelectric, inductive, and fiber optic pressure sensors, helping you make the most informed choice among many options.
Piezoresistive Pressure Sensors
Definition and Working Principle
Piezoresistive pressure sensors measure pressure through changes in resistance caused by applied pressure. The working principle is based on the piezoresistive effect, where the resistance of a material changes when it undergoes mechanical deformation (such as pressure). Typically, piezoresistive pressure sensors are made of silicon, ceramic, or metal films. When pressure is applied to these materials, their resistance changes are converted into electrical signals.
Application Scenarios
Piezoresistive pressure sensors are widely used in various industrial fields, such as automotive, medical devices, household appliances, and industrial automation. In the automotive industry, they measure engine oil pressure and tire pressure. In medical devices, they are used to measure blood pressure and respiratory system pressure. In industrial automation, piezoresistive sensors monitor pressure in hydraulic and pneumatic systems.
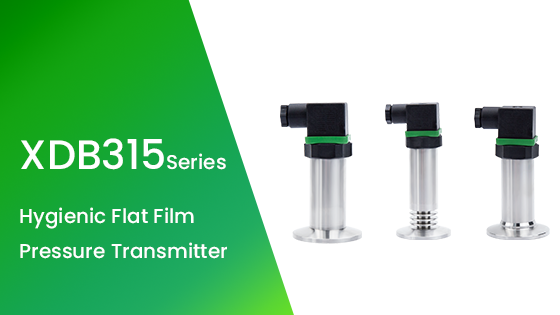
The XDB series piezoresistive pressure sensors, such as the XDB315 and XDB308 series, further expand the possibilities of these applications. The XDB315 series pressure transmitters use high-precision and high-stability diffused silicon flat film sanitary diaphragms, featuring anti-blocking functions, long-term reliability, and high accuracy, making them particularly suitable for industries with high sanitary requirements, such as food and pharmaceuticals. The XDB308 series pressure transmitters, with advanced piezoresistive sensor technology and various signal output options, provide excellent long-term stability, suitable for various media and environments compatible with SS316L.
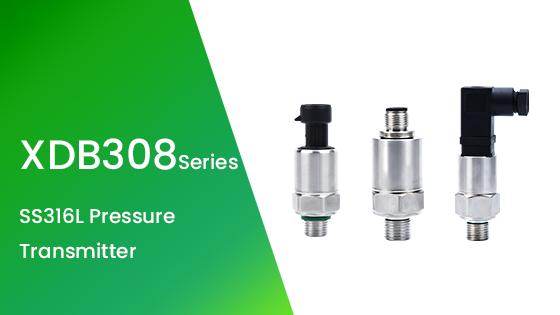
Advantages and Disadvantages
Piezoresistive pressure sensors offer high accuracy, good linearity, and fast response time. Additionally, they are typically small in size and suitable for space-constrained applications. However, these sensors also have some drawbacks, such as sensitivity to temperature changes, which may require temperature compensation. Moreover, their long-term stability in high-pressure applications may not be as good as other types of sensors.
Capacitive Pressure Sensors
Definition and Working Principle
Capacitive pressure sensors detect pressure by measuring changes in capacitance caused by applied pressure. These sensors typically consist of two parallel electrode plates. When pressure is applied, the distance between these plates changes, resulting in a change in capacitance. The capacitance change is then converted into readable electrical signals.
Application Scenarios
Capacitive pressure sensors are widely used in liquid-level measurement, gas detection, and vacuum systems. In liquid level measurement, they determine the level by measuring changes in liquid height. In gas detection, they measure gas pressure and flow. In vacuum systems, they monitor internal pressure changes.
The XDB602 series capacitive pressure/differential pressure transmitters, with modular microprocessor design and advanced digital isolation technology, ensure exceptional stability and resistance to interference. Built-in temperature sensors improve measurement accuracy and reduce temperature drift, along with robust self-diagnostic capabilities, making them ideal for high-precision applications in industrial automation and process control.
Advantages and Disadvantages
Capacitive pressure sensors offer high sensitivity, low power consumption, and good temperature stability. Additionally, their simple structure gives them a long lifespan. However, they are sensitive to humidity changes and may require additional protection in high-humidity environments. Furthermore, capacitive sensors may not perform well in high-pressure applications.
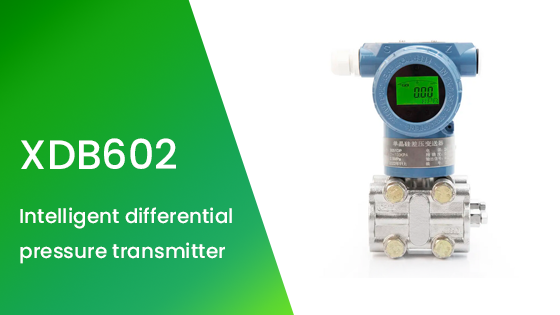
Piezoelectric Pressure Sensors
Definition and Working Principle
Piezoelectric pressure sensors measure pressure using the piezoelectric effect, where certain crystalline materials generate electric charges when subjected to mechanical pressure. These materials typically include quartz, barium titanate, and piezoelectric ceramics. When pressure is applied, they produce electrical signals proportional to the applied pressure.
Application Scenarios
Piezoelectric pressure sensors are widely used in dynamic pressure measurement, such as impact testing, explosion research, and vibration measurement. In the aerospace and automotive industries, they measure engine combustion pressure and shock waves. In industrial automation, they monitor vibrations and mechanical stress.
Advantages and Disadvantages
Piezoelectric pressure sensors offer high-frequency response, good dynamic performance, and high sensitivity, making them suitable for measuring rapidly changing pressures. However, they cannot be used for static pressure measurement as they cannot maintain a charge over time. They are also sensitive to temperature changes and may require temperature compensation.
Inductive Pressure Sensors
Definition and Working Principle
Inductive pressure sensors detect pressure by measuring changes in inductance caused by applied pressure. These sensors usually consist of an inductive coil and a movable core. When pressure is applied, the core's position changes, altering the inductance of the coil. The inductance change is then converted into readable electrical signals.
Application Scenarios
Inductive pressure sensors are mainly used in high-temperature environments and harsh industrial settings, such as turbine pressure monitoring and high-temperature fluid systems. In the oil and gas industry, they measure downhole pressure. In industrial automation, they monitor the pressure of high-temperature gases and liquids.
Advantages and Disadvantages
Inductive pressure sensors offer good temperature stability and high accuracy, suitable for high-temperature and harsh environments. Their robust structure provides long-term reliability. However, these sensors are relatively large and may not be suitable for space-constrained applications. Additionally, their response speed is relatively slow, making them less suitable for rapidly changing pressure measurements.
Fiber Optic Pressure Sensors
Definition and Working Principle
Fiber optic pressure sensors detect pressure by measuring changes in light signals caused by applied pressure. These sensors use variations in light intensity, phase, or wavelength within the optical fiber to reflect pressure changes. When pressure is applied to the fiber, its physical properties change, altering the light signals.
Application Scenarios
Fiber optic pressure sensors are widely used in medical, environmental monitoring, and oil exploration fields. In the medical field, they measure blood pressure and internal body pressure. In environmental monitoring, they detect ocean and groundwater pressures. In oil exploration, they measure pressure during drilling processes.
Advantages and Disadvantages
Fiber optic pressure sensors offer immunity to electromagnetic interference, suitability for long-distance measurements, and high sensitivity. Their material properties allow them to operate stably in harsh environments. However, these sensors are costly, and their installation and maintenance are complex. They are also sensitive to mechanical damage, requiring careful handling and protection.
By understanding the working principles, application scenarios, and advantages and disadvantages of different types of pressure sensors by technology, we can make more informed choices for specific applications, ensuring that the selected sensors meet the requirements and improve system reliability and efficiency.
Post time: Jul-12-2024