Introduction
Imagine when you are inflating your bicycle tires with an air pump in the garage or cleaning dust in the yard with a jet gun, do you realize the key technology behind these tools? These convenient devices in our daily lives rely on a mechanical device called an air compressor. An air compressor is a mechanical device that compresses air to increase its pressure, widely used in both industrial and home environments. In the industrial field, air compressors are used to operate pneumatic tools, automation equipment, spray painting, and other applications requiring high-pressure air. Air compressors are often used in home environments for inflation, cleaning, and some simple DIY projects. Due to their versatility and efficiency, air compressors play an important role in modern life.
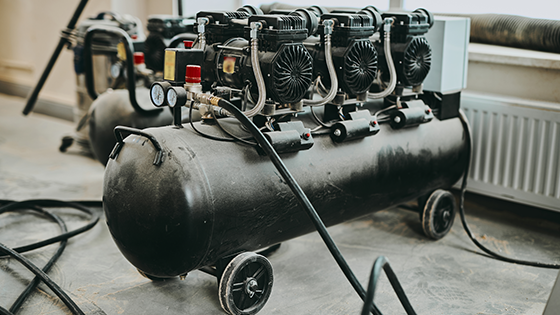
A pressure switch is one of the key components in an air compressor, and its main function is to monitor and control the pressure inside the air compressor. The pressure switch senses pressure changes within the compressor and automatically turns the compressor circuit on or off when the preset pressure value is reached, ensuring the compressor operates within a safe and efficient range. Proper installation and adjustment of the pressure switch can prevent equipment damage and safety hazards caused by excessive pressure, while also improving the compressor's efficiency and lifespan.
1. Basic Principles of an Air Compressor Pressure Switch
Definition and Function
A pressure switch is an electrical device used to monitor and control the pressure inside an air compressor. Its primary function is to automatically switch the circuit on or off when the compressor reaches the preset pressure level, starting or stopping the compressor's operation. This automated control ensures that the compressor works within a safe pressure range, preventing equipment damage and safety hazards due to excessive pressure.
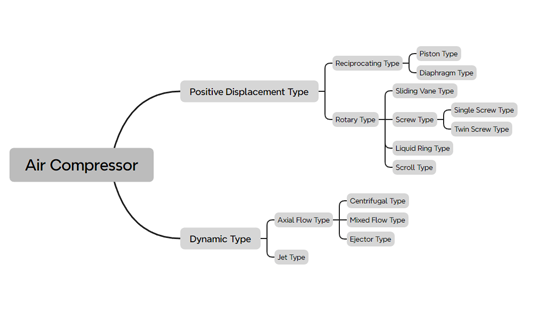
Working Principle of the Pressure Switch
The working principle of the pressure switch is based on the pressure sensor monitoring the internal pressure of the system. The basic steps are as follows:
1. Pressure Detection: The built-in pressure sensor of the pressure switch monitors the air pressure inside the air compressor in real-time. When the pressure reaches the preset upper limit, the sensor sends a signal to the switch control device.
2. Circuit Switching: Upon receiving the pressure signal, the electrical contacts of the pressure switch automatically open, cutting off the compressor's power, and stopping its operation. This process prevents the compressor from continuing to pressurize, avoiding excessive pressure.
3. Pressure Drop: As the compressor stops working, the air pressure inside the system gradually decreases. When the pressure drops to the preset lower limit, the pressure sensor sends another signal.
4. Restart: After receiving the pressure drop signal, the electrical contacts of the pressure switch close again, restoring the power supply to the compressor, which then restarts and begins working.
This automated pressure control mechanism not only ensures the efficient operation of the air compressor but also enhances the system's safety and reliability.
2. Components of the Pressure Switch
Pressure Sensor
The pressure sensor is the core component of the pressure switch, responsible for real-time monitoring of the pressure inside the air compressor. Depending on the sensor type, common pressure sensors include mechanical and electronic types:
1. Mechanical Pressure Sensors: Utilize mechanical elements such as springs or diaphragms to respond to pressure changes. When the pressure reaches the preset value, the mechanical structure triggers the action of the electrical contacts.
2. Electronic Pressure Sensors: Use piezoelectric, resistive strain gauge, or capacitive sensing elements to convert pressure changes into electrical signals. These signals are processed by electronic circuits to control the switching of electrical contacts.
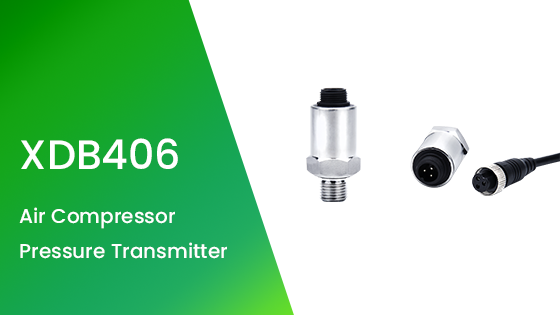
XDB406 series pressure transmitter is ideal for air compressor applications, offering high accuracy, durability, and easy integration. It ensures precise pressure monitoring and control, enhancing the safety and efficiency of air compressors in both industrial and home environments. The transmitter's robust design and advanced sensing technology make it a reliable choice for maintaining optimal compressor performance.
Electrical Contacts
The electrical contacts are the part of the pressure switch responsible for circuit switching. They operate based on the pressure sensor's signals and have the following primary functions:
1. Power Control: When the pressure sensor detects that the pressure has reached the upper limit, the electrical contacts cut off the compressor's power, stopping its operation. When the pressure drops to the lower limit, the contacts close, starting the compressor.
2. Signal Transmission: The state changes of the electrical contacts are transmitted through signal lines to the control system or other related equipment, ensuring coordinated system operation.
Mechanical Components
Mechanical components include the pressure switch's structural housing, adjustment mechanisms, and connectors, ensuring the pressure switch's stability and reliability. The main mechanical components are:
1. Housing: Provides protection and support, preventing damage to internal electronic and mechanical components from external environments.
2. Adjustment Mechanism: Usually composed of screws or knobs, it sets the pressure switch's upper and lower pressure values. The adjustment mechanism allows users to adjust the pressure switch's working range according to specific application needs.
3. Connectors: Include interfaces for connecting to the compressor and power supply, ensuring a tight connection and stable operation of the pressure switch with the system.
Through the coordinated work of these components, the pressure switch can accurately monitor and control the air pressure inside the compressor, ensuring the system operates within a safe and effective range.
3. Different Types of Pressure Switches
Mechanical Pressure Switches
Mechanical pressure switches rely on physical force to detect and respond to pressure changes. Their working principle typically involves the movement of a spring or diaphragm under pressure, triggering the opening or closing of electrical contacts. Mechanical pressure switches are widely used due to their simple design, low cost, and ease of maintenance. They are suitable for applications requiring stability and durability, such as traditional industrial equipment and home air compressors.
Electronic Pressure Switches
Electronic pressure switches use sensors to convert pressure changes into electrical signals and control the switch's state through electronic circuits. Common electronic pressure sensors include piezoelectric sensors and resistive strain gauge sensors. Electronic pressure switches are characterized by high precision, fast response, and a wide adjustable range, making them suitable for applications requiring precise control, such as precision machinery and automation systems.
Digital Pressure Switches
Digital pressure switches combine electronic sensing technology with digital display technology, providing more intuitive pressure readings and flexible control methods. Users can set and read pressure values through a digital interface, and some models also have data recording and remote monitoring functions. Digital pressure switches are suitable for modern industrial and technological fields, such as smart manufacturing and IoT applications.
4. Working Process of the Pressure Switch
Trigger Conditions for Switching States
The pressure switch's state switching is based on preset pressure thresholds. When the pressure reaches or exceeds the upper threshold, the pressure sensor sends a signal to trigger the switch action, cutting off the power; when the pressure drops to the lower threshold, the sensor sends another signal, closing the switch and restoring the power.
Pressure Detection and Signal Transmission
The pressure sensor continuously monitors the air pressure inside the air compressor. The detected pressure signal is converted into a processable electrical signal by the sensor circuit. These signals are transmitted to the control unit, which decides whether to switch the state of the switch.
Opening and Closing of Electrical Circuits
Based on the pressure signal, the switch controls the state of the electrical contacts. When the pressure reaches the upper limit, the contacts open the circuit, stopping the compressor's operation; when the pressure drops to the lower limit, the contacts close the circuit, starting the compressor. This process ensures the system operates within a safe pressure range.
5. Installation and Adjustment of the Pressure Switch
Installation Position and Steps
1. Choose an Appropriate Location: Ensure the installation location is conducive to pressure detection and safe.
2. Fix the Switch: Use appropriate tools to secure the pressure switch in the selected location.
3. Connect Pipes and Power Supply: Properly connect the pressure switch to the compressor's pressure pipe and power supply, ensuring no leaks and electrical safety.
Method for Adjusting Pressure Range
1. Set Upper-Pressure Limit: Use the adjustment screw or digital interface to set the compressor's maximum working pressure.
2. Set Lower Pressure Limit: Use the same method to set the compressor's minimum working pressure, ensuring the compressor operates within the ideal pressure range.
Common Problems and Solutions
1. Inaccurate Pressure Settings: Recalibrate the pressure switch to ensure accurate settings.
2. Frequent Switching: Check for leaks in the compressor and piping system, and adjust the pressure range settings.
3. Switch Malfunction: Check the electrical connections and sensor status, and replace damaged components if necessary.
6. Maintenance and Care of the Pressure Switch
Regular Inspection and Testing Regularly inspect and test the pressure switch to ensure its normal operation. This includes calibrating the pressure sensor, cleaning electrical contacts, and lubricating mechanical components.
Troubleshooting Common Faults
1. Sensor Failure: Check and replace damaged sensors.
2. Burnt Electrical Contacts: Clean or replace burnt contacts.
3. Worn Mechanical Parts: Regularly inspect and replace worn mechanical parts.
By following these guidelines, the pressure switch can maintain optimal performance, ensuring the safe and efficient operation of the air compressor.
Post time: Jul-19-2024