In pressure measurement, you may notice that the measurement results do not immediately reflect changes in input pressure or fully correspond when the pressure returns to its initial state. For example, when using a bathroom scale to measure weight, the scale's sensor requires time to accurately sense and stabilize the reading of your weight. The response time of the sensor leads to initial data fluctuations. Once the sensor adjusts to the load and completes the data processing, the readings will display more stable results. This is not a defect of the sensor but a normal characteristic of many electronic measurement devices, especially when involving real-time data processing and steady-state achievement. This phenomenon can be referred to as sensor hysteresis.
What is hysteresis in pressure sensors?
Sensor hysteresis typically manifests when there is a change in input (such as temperature or pressure), and the output signal does not immediately follow the input change, or when the input returns to its original state, the output signal does not fully revert to its initial state. This phenomenon can be seen on the sensor's characteristic curve, where there is a lagging loop-shaped curve between input and output, rather than a straight line. Specifically, if you start increasing the input from a certain specific value, the sensor's output will also increase accordingly. However, when the input begins to decrease back to the original point, you will find that the output values are higher than the original output values during the reduction process, forming a loop or hysteresis loop. This shows that during the increasing and decreasing process, the same input value corresponds to two different output values, which is the intuitive display of hysteresis.
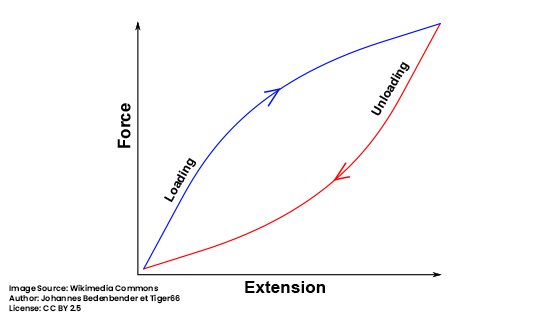
The diagram shows the relationship between output and applied pressure in a pressure sensor during the pressure application process, represented in the form of a hysteresis curve. The horizontal axis represents sensor output, and the vertical axis represents applied pressure. The red curve represents the process where the sensor output increases with gradually increasing pressure, showing the response path from low to high pressure. The blue curve indicates that as the applied pressure begins to decrease, the sensor output also decreases, from high pressure back to low, depicting the sensor's reaction during the unloading of pressure. The area between the two curves, the hysteresis loop, displays the difference in sensor output at the same pressure level during loading and unloading, typically caused by the physical properties and internal structure of the sensor material.
Reasons for Pressure Hysteresis
The hysteresis phenomenon in pressure sensors is mainly influenced by two major factors, which are closely related to the physical properties and operating mechanism of the sensor:
- Material's elastic hysteresis Any material will undergo a certain degree of elastic deformation when subjected to external forces, a direct response of the material to the forces applied. When the external force is removed, the material attempts to return to its original state. However, this recovery is not complete due to the non-uniformity within the material's internal structure and the slight irreversible changes in the internal microstructure during repeated loading and unloading. This results in a lag in mechanical behavior output during continuous loading and unloading processes, known as elastic hysteresis. This phenomenon is particularly evident in the application of pressure sensors, as sensors often need to measure and respond to pressure changes accurately.
- Friction In the mechanical components of a pressure sensor, especially those involving moving parts, friction is inevitable. This friction may come from contacts within the sensor, such as sliding contact points, bearings, etc. When the sensor bears pressure, these friction points can hinder the free movement of the sensor's internal mechanical structures, causing a delay between the sensor's response and the actual pressure. When the pressure is unloaded, the same friction forces may also prevent the internal structures from stopping immediately, thus also displaying hysteresis during the unloading phase.
These two factors together lead to the hysteresis loop observed in sensors during repeated loading and unloading tests, a characteristic that is often of particular concern in applications where precision and repeatability are highly demanded. To reduce the impact of this hysteresis phenomenon, careful design and material selection for the sensor is crucial, and software algorithms may also be needed to compensate for this hysteresis in applications.
The hysteresis phenomenon in pressure sensors is influenced by various factors directly related to the sensor's physical and chemical properties and its operating environment.
What factors lead to sensor hysteresis?
1. Material properties
- Elastic modulus: The material's elastic modulus determines the degree of elastic deformation when subjected to force. Materials with a higher elastic modulus deform less, and their elastic hysteresis might be relatively lower.
- Poisson's ratio: Poisson's ratio describes the ratio of lateral contraction to longitudinal elongation in a material when subjected to force, which also affects the material's behavior during loading and unloading.
- Internal structure: The material's microstructure, including crystal structure, defects, and inclusions, affects its mechanical behavior and hysteresis characteristics.
2. Manufacturing process
- Machining precision: The precision of sensor component machining directly affects its performance. Components with higher precision fit better, reducing additional friction and stress concentration caused by poor fit.
- Surface roughness: The quality of surface treatment, such as surface roughness, affects the magnitude of friction, thereby influencing the sensor's response speed and hysteresis.
- Temperature changes affect the physical properties of materials, such as the elastic modulus and friction coefficient. High temperatures generally make materials softer, reducing the elastic modulus and increasing friction, thereby increasing hysteresis. Conversely, low temperatures may make materials harder and more brittle, affecting hysteresis in different ways.
3. Temperature
- Temperature changes affect the physical properties of materials, such as the elastic modulus and friction coefficient. High temperatures generally make materials softer, reducing the elastic modulus and increasing friction, thereby increasing hysteresis. Conversely, low temperatures may make materials harder and more brittle, affecting hysteresis in different ways.
Risks
The presence of hysteresis in pressure sensors can cause measurement errors, affecting the accuracy and reliability of the sensor. In applications requiring high-precision measurements, such as precision industrial process control and critical medical equipment monitoring, hysteresis can lead to significant measurement errors and even cause the entire measurement system to fail. Therefore, understanding and minimizing the impact of hysteresis is a key part of ensuring the efficient and accurate operation of pressure sensors.
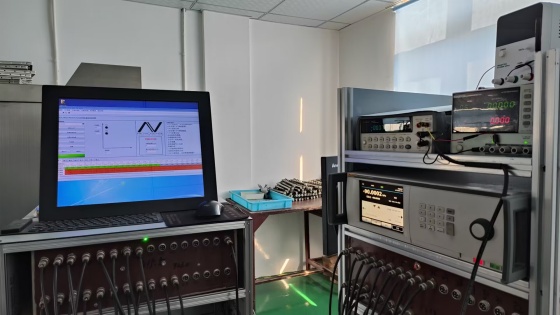
Solutions for Hysteresis in Pressure Sensors:
To ensure the lowest possible hysteresis effects in pressure sensors, manufacturers have taken several key measures to optimize sensor performance:
- Material selection: The choice of materials plays a decisive role in hysteresis. Therefore, manufacturers carefully select core materials used in sensor construction, such as diaphragms, seals, and fill fluids, to ensure they exhibit minimal hysteresis under different working conditions.
- Design optimization: By improving the structural design of sensors, such as the shape, size, and thickness of diaphragms, and optimizing sealing methods, manufacturers can effectively reduce hysteresis caused by friction, static friction, and material deformation.
- Aging treatment: Newly manufactured sensors may exhibit significant initial hysteresis. Through aging treatment and specific testing programs, materials can be accelerated to stabilize and adapt, thus reducing this initial hysteresis. The image below shows the XDB305 undergoing aging treatment.
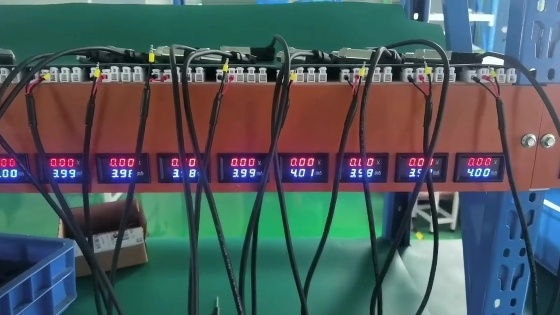
- Strict production control: By strictly controlling tolerances and quality during the production process, manufacturers ensure the consistency of each sensor and minimize the impact of production variations on hysteresis.
- Advanced calibration and compensation: Some manufacturers use advanced digital compensation technology and multi-point calibration methods to precisely model and correct the hysteresis in sensor outputs.
- Performance testing and grading: All sensors undergo detailed testing to assess their hysteresis characteristics. Based on the test results, sensors are graded to ensure that only products meeting specific hysteresis standards are released to the market.
- Accelerated life testing: To verify the performance stability of sensors throughout their expected lifespan, manufacturers conduct accelerated aging and life tests on samples to ensure that hysteresis remains within acceptable limits.
These comprehensive measures help manufacturers effectively control and reduce the hysteresis phenomenon in pressure sensors, ensuring that the sensors meet high accuracy and reliability requirements in actual applications.
Post time: May-09-2024