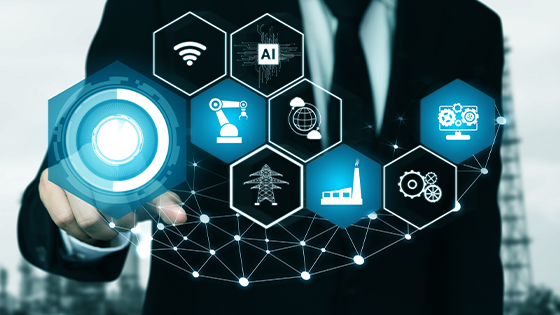
Since Germany first introduced the concept of "Industry 4.0" in 2011, smart manufacturing has gradually become a key development direction for global manufacturing industries. In simple terms, smart manufacturing involves applying advanced technologies like big data, artificial intelligence (AI), and the Internet of Things (IoT) to the production process, making factories smarter, more efficient, and more flexible. Imagine a future factory as a "brain" that can think for itself, automatically adjusting production rhythms based on real-time data and even detecting and fixing problems on its own.
In the past industrial era, traditional manufacturing models relied heavily on manual labor and mechanized equipment. The production process was often linear and fixed, with each step—from raw material procurement to production, inspection, and delivery—being strictly controlled and monitored by humans. While this ensured a certain scale of production, it also led to inefficiencies, bottlenecks in productivity, and resource waste. Additionally, the "information silos" between equipment meant they could not communicate or collaborate like today’s smart systems, resulting in delayed decision-making due to the lack of real-time information.
The emergence of smart manufacturing broke this model, connecting equipment, personnel, and information systems through IoT technology. Every step in the manufacturing process—from raw materials entering the factory, to the operating status of machines, to every detail on the production line—is monitored in real-time through sensors. This data is not only used for immediate production scheduling but is also analyzed using big data for predictive maintenance, preventing downtime by identifying faults before they cause disruptions. Furthermore, AI and machine learning are incorporated to adjust production plans based on real-time data, optimizing production efficiency.
In this way, smart manufacturing not only improves production efficiency but also enhances flexibility and precision through deep integration of data. Unlike the traditional, "fixed-mode" approach, smart manufacturing allows production lines to quickly adapt to market demand, enabling customized and flexible production. Simply put, smart manufacturing uses technology to make factories "live" production systems, capable of self-sensing, thinking, and decision-making.
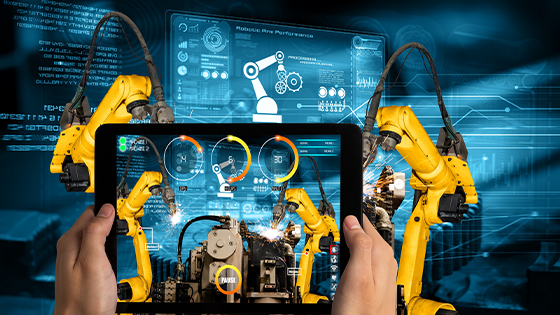
The Application of Smart Manufacturing: From Automation to Intelligence
The core of smart manufacturing is primarily reflected in the application of automation technologies. Today, automated equipment, robots, and smart warehousing systems are widely used in factories around the world. The production processes that once required a large workforce can now be completed by robots and automated production lines. For example, robots can perform precise welding and assembly tasks on the production line, while automated systems can handle product classification, packaging, and delivery. Many of the repetitive, tedious tasks in production are now taken over by automation, freeing up human labor and boosting efficiency.
But the true charm of smart manufacturing goes beyond just automation. Automation is the starting point, while the essence of smart manufacturing lies in its intelligence. As IoT technology develops, the connectivity between equipment and systems becomes even more seamless. Every machine, every production line, is no longer "isolated." They communicate with each other through sensors and data collection systems, providing real-time feedback on production data. This data, processed through cloud platforms or local servers, enables more precise production scheduling and maintenance planning. For instance, if a machine is malfunctioning, the system will immediately send an alert, perform a diagnostic, and even guide maintenance personnel to make quick repairs.
Additionally, AI and machine learning further enhance the intelligence of production systems. By analyzing big data, the system not only monitors production in real time but can also predict future production needs based on historical data, helping enterprises plan production schedules in advance, avoiding resource waste and bottlenecks. In some advanced manufacturing sectors, AI can continuously optimize production processes by learning from data, improving product quality and consistency.
Despite the many advantages of smart manufacturing, there are still challenges in its practical application. First, the technological infrastructure required for smart manufacturing is quite demanding, necessitating significant investment in information technology and automation. For small and medium-sized enterprises (SMEs), such investment may seem daunting. Secondly, compatibility issues between traditional equipment and modern smart systems continue to pose a challenge. In some older production lines, equipment cannot interface with smart systems, creating barriers to information flow and data silos. Moreover, while smart manufacturing allows for efficient, flexible production, its implementation also increases the complexity of technology and requires higher skill levels from workers, posing greater demands on employee training and technical support.
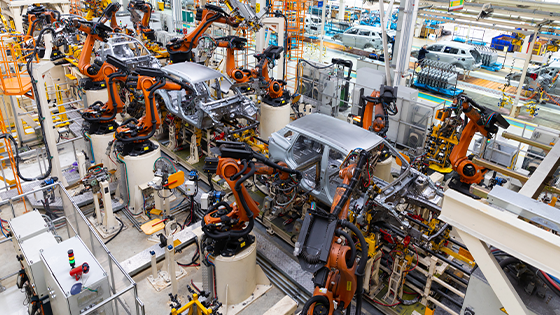
Future Outlook: The Infinite Potential of Smart Manufacturing
Although smart manufacturing faces some challenges today, its future is filled with limitless possibilities. With continuous advancements in technology, especially in AI, 5G communication, and cloud computing, smart manufacturing will further transform the manufacturing landscape. Future factories will no longer be just production lines, but rather smart, flexible, and highly automated systems. These factories will be capable of responding to market demands in real time, optimizing production processes autonomously, and even achieving personalized customization and small-batch production.
First, the widespread adoption of 5G technology will enable the broader application of the Industrial Internet of Things (IIoT), bringing faster communication speeds and lower latency. This means that manufacturing industries will be able to achieve more real-time data transmission and equipment management. Enterprises will be able to monitor the production status of factories globally in real time via cloud platforms, making timely adjustments to ensure efficiency and quality.
Additionally, the further development of AI will push manufacturing toward a more "intelligent" future. AI will not only help enterprises with predictive maintenance and production process optimization, but it will also process and analyze data through deep learning, providing more accurate decision-making support. Future factories will be able to self-adjust production rhythms through AI, even optimizing production schedules autonomously based on market changes, achieving truly "intelligent" decision-making.
Furthermore, with the rise of the "green manufacturing" concept, smart manufacturing will also play a key role in energy efficiency, resource optimization, and sustainability. Through smart devices and systems, enterprises will be able to use energy more efficiently, reduce resource waste, and implement environmentally-friendly production models. This will not only help enterprises lower costs but also drive the entire industry toward sustainable development.
Overall, the future of smart manufacturing is not just about technological advancements but also about industry upgrading and societal development. As technology continues to mature and become more widely adopted, smart manufacturing will become the mainstream of global manufacturing, driving more efficient, sustainable, and intelligent global supply chains.
Conclusion: Smart Manufacturing, Leading the Future
Smart manufacturing has not only transformed traditional manufacturing models but also brought unprecedented possibilities for the future of industry. As technology progresses, manufacturing will become smarter, more efficient, and more flexible. While challenges remain, the future of smart manufacturing is bright. It will undoubtedly continue to lead global manufacturing toward a smarter and more sustainable future.
About XIDIBEI
XIDIBEI is a professional pressure sensor manufacturer dedicated to providing high-quality and reliable sensor products to customers worldwide. With extensive experience in the automotive, industrial, and energy sectors, we continuously innovate to help various industries achieve smarter and more digital futures. XIDIBEI’s products are sold globally and have earned widespread acclaim from customers. We uphold the philosophy of "technology first, service excellence" and are committed to providing superior service to our global clients.
For more information, visit our website: http://www.xdbsensor.com or contact us via email at info@xdbsensor.com.
Post time: Jan-07-2025