Introduction to Ceramic Pressure Sensors
Ceramic pressure sensors represent a significant advancement in the field of sensor technology, offering unmatched durability and precision. These sensors play a crucial role in various industries, from automotive to healthcare, accurately measuring pressure levels in diverse environments. This article delves into their operating principles, highlighting their importance and widespread applications.
Understanding Pressure Sensors
Pressure sensors are key components in modern technology, used to measure the force exerted by liquids or gases. There are several types, each with its unique principles and applications. Among these, ceramic pressure sensors stand out for their robustness and precision.
The Foundation of Ceramic Materials in Sensing
Ceramic materials play a fundamental role in the sensing domain. They are renowned for their exceptional strength, stability, and ability to withstand harsh conditions. These characteristics make ceramic materials highly suitable for various sensing applications where reliability is crucial.
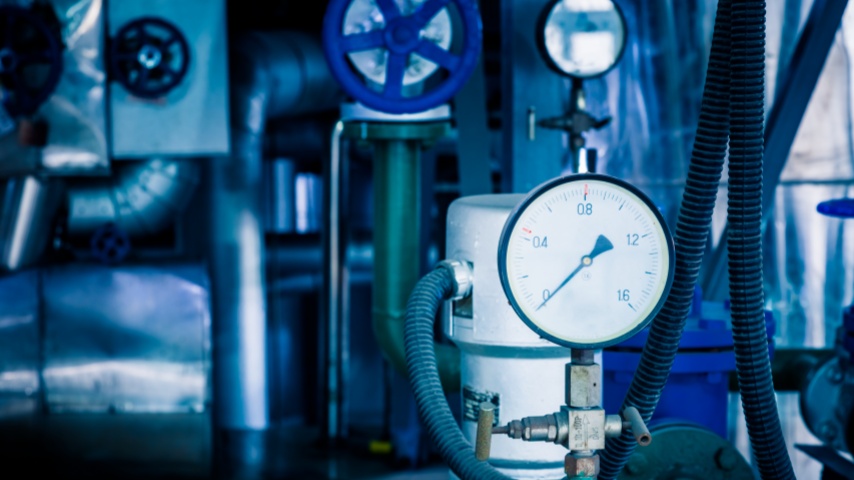
Primary applications of ceramic materials in sensing include:
1. Pressure Sensors: Ceramic pressure sensors utilize the piezoelectric effect to convert pressure into an electrical signal. They are known for their high accuracy, durability, and stability, making them widely used in the automotive, medical, industrial, and aerospace sectors.
2. Temperature Sensors: Ceramic temperature sensors exploit the property of ceramic materials' resistance to changing temperatures. They offer high accuracy, a broad measuring range, and stability, finding applications in industrial, medical, and environmental monitoring.
3. Flow Sensors: Ceramic flow sensors leverage the piezoelectric effect or acoustic properties of ceramic materials. Capable of measuring the flow of liquids or gases, they are appreciated for their accuracy, wide range, and stability, and are employed in industrial, agricultural, and environmental monitoring.
How ceramic pressure sensors work
The working principle of ceramic pressure sensors is based on the principle of deformation caused by pressure. These sensors typically operate on piezoresistive or capacitive principles, converting mechanical pressure into an electrical signal.
Piezoresistive ceramic pressure sensors utilize the piezoresistive effect, where the material's resistance changes with applied pressure. When pressure is applied to a ceramic diaphragm, it deforms, causing a change in the resistance of pressure-sensitive resistors on the diaphragm. This change in resistance is converted into a voltage signal proportional to the pressure through a Wheatstone bridge.
Capacitive ceramic pressure sensors exploit the characteristic that the dielectric constant of ceramic materials changes with applied pressure. When pressure is applied to a ceramic diaphragm, it deforms, altering the distance between the ceramic diaphragm and a metal substrate, thus changing the capacitance of the capacitor. These changes in capacitance are converted into a voltage signal proportional to the pressure through conditioning circuits.
How Ceramic Pressure Sensors Measure Pressure
Ceramic pressure sensors measure pressure by detecting the deformation of ceramic elements and converting these changes into measurable and analyzable electrical signals. These sensors typically include several core components: ceramic elements, metal substrates, and electrodes. The ceramic element, the key part of the sensor, is usually made from materials with piezoelectric effects, such as alumina or lead zirconate titanate. The metal substrate supports the ceramic element and provides electrical connections, while electrodes collect the electrical signals produced by the ceramic element. When pressure is applied to the ceramic element, it deforms, generating an electrical signal through the change in piezoelectric effect, which is proportional to the applied pressure. The output signal of ceramic pressure sensors can be measured through piezoresistive measurement (using a Wheatstone bridge to convert resistance changes into a voltage signal) or capacitive measurement (using conditioning circuits to convert capacitance changes into a voltage signal).
Advantages of Ceramic Pressure Sensors
Ceramic pressure sensors are particularly suited to harsh application environments due to their numerous advantages. These sensors stand out for their high accuracy (with precision up to 0.1% or higher), wide operating temperature range (from -40°C to +200°C), strong corrosion resistance (able to withstand acids, bases, salts, and other corrosive media), high durability, and good stability. Furthermore, ceramic pressure sensors can measure a very wide range of pressures, offering higher accuracy, a wider operating temperature range, and stronger corrosion resistance than metal pressure sensors, and they offer a higher cost-performance ratio compared to other types of pressure sensors.
These characteristics make ceramic pressure sensors widely used in various industries such as automotive (for measuring tire pressure, engine pressure, etc.), healthcare (for blood pressure and blood flow measurement), industrial (for hydraulic and gas pressure measurement), and aerospace (for measuring aircraft altitude and speed, etc.). This broad applicability and excellent performance demonstrate the unparalleled value of ceramic pressure sensors in facing various challenges.
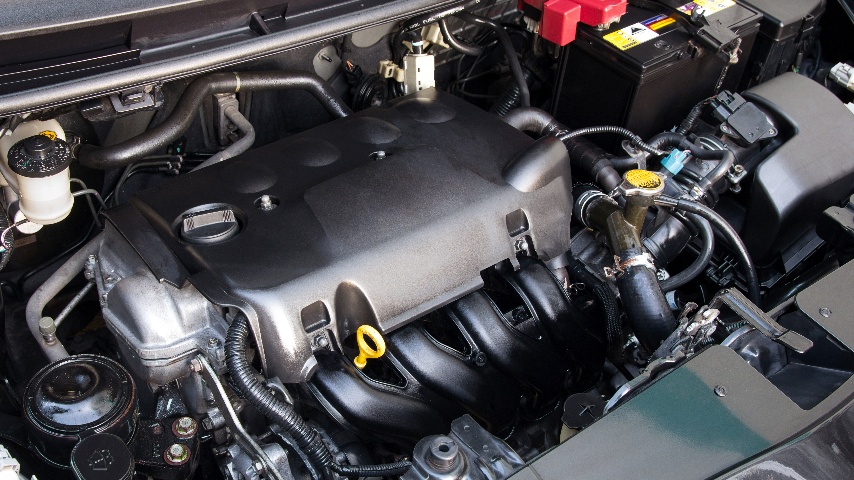
Innovation in Ceramic Pressure Sensor Technology
The continuous development and progress in the field of ceramic pressure sensors have significantly enhanced their performance and expanded their application range. These advancements are primarily reflected in the development of new ceramic materials, the application of new manufacturing processes, and the development of new designs. New materials like alumina, lead zirconate titanate, and silicon nitride have improved the sensor's accuracy, temperature resistance, corrosion resistance, and impact resistance. At the same time, the introduction of Micro-Electro-Mechanical Systems (MEMS) technology has improved accuracy, sensitivity, and reliability, while new designs, such as thin-film ceramic pressure sensors, have effectively reduced costs and sizes. These innovations not only meet more demanding application requirements but also make ceramic pressure sensors widely used in the automotive, medical, industrial, and aerospace sectors. With ongoing technological innovation, it is expected that the future of ceramic pressure sensors will see further performance improvements and an expansion of their application range to meet the needs of more industries.
Challenges and Solutions in Ceramic Sensing Technology
Although ceramic pressure sensors have many advantages, they also face some challenges, such as high sensitivity to vibration due to the brittleness of ceramic materials and sensitivity to temperature changes, which may affect their performance. Additionally, compared to metal pressure sensors, the cost of ceramic pressure sensors is usually higher, limiting their widespread use in some applications.
To overcome these challenges, continuous innovations and technological improvements are being developed within the industry. These include the use of new ceramic materials to improve toughness and reduce temperature sensitivity, improvements in manufacturing processes to enhance vibration resistance, and the application of compensation techniques to mitigate the effects of temperature changes. These efforts have significantly enhanced the performance of ceramic pressure sensors, enabling their use in a broader range of fields.
Specific solutions include using ceramic materials with higher toughness (such as alumina and silicon nitride), improving designs to reduce sensor mass and increase rigidity, and using vibration isolation technologies like rubber pads or springs to isolate vibrations. For temperature sensitivity issues, temperature compensation techniques and the selection of materials with lower temperature sensitivity (such as zirconia and barium titanate) can be employed. Meanwhile, to address cost issues, improvements in manufacturing processes and the development of new sensor technologies, such as thin-film technology, can effectively reduce costs.
Looking to the future, the continued development of ceramic sensing technology is expected to further enhance the performance, reliability, and cost-effectiveness of ceramic pressure sensors, driving their application and popularization in more fields. These technological advances not only address existing challenges but also open new possibilities for the future applications of ceramic pressure sensors.
Choosing the Right Ceramic Pressure Sensor
When selecting the appropriate ceramic pressure sensor, it is essential to consider multiple key factors to ensure the sensor meets the specific requirements of the application. First, the choice of measuring range is crucial and must be determined based on the application's needs to ensure the sensor can cover the required pressure range. Second, accuracy is also an important consideration and sensors with the appropriate accuracy level should be selected based on the application's requirements for measurement precision.
Beyond basic measurement needs, environmental conditions play a decisive role in choosing the right ceramic pressure sensor. The specific requirements of the application environment, such as temperature resistance and corrosion resistance, have a direct impact on sensor performance. Therefore, when selecting a sensor, it is necessary to consider whether it can operate stably under specific environmental conditions, such as high temperatures, high pressures, or corrosive environments.
For applications with small measurement ranges and high accuracy requirements, high-accuracy sensors should be prioritized. For applications with larger measurement ranges, sensors with a wider range should be selected. For those applications in high-temperature, high-pressure, or corrosive environments, choosing sensors that can withstand these harsh conditions is particularly critical. Such comprehensive consideration not only ensures the sensor's applicability and reliability but also maintains efficiency and precision in long-term operation.
The Future of Ceramic Pressure Sensors
Looking ahead, the future of ceramic pressure sensors is very promising, thanks to continuous research and technological progress. This field is expected to witness broader applications and enhanced performance. With the development of new ceramic materials, such as those with higher precision, wider operating temperature ranges, stronger corrosion resistance, and lower costs, the performance of ceramic pressure sensors will be significantly improved. The advancement of these materials provides a better foundation for sensors, enabling them to more effectively meet various challenges.
Additionally, new manufacturing processes, such as the application of Micro-Electro-Mechanical Systems (MEMS) technology, are expected to further improve the accuracy, sensitivity, reliability, and yield of ceramic pressure sensors. These technological advancements not only optimize the production process but also enhance the overall performance of sensors, enabling them to meet stricter application requirements. Furthermore, the adoption of new design concepts, such as thin-film ceramic pressure sensors, will further reduce costs and sizes, making ceramic pressure sensors easier to integrate and use.
These development trends indicate that ceramic pressure sensors will find even broader applications in the automotive, medical, industrial, and aerospace fields. In the automotive industry, they can be used to measure tire pressure, engine pressure, and brake pressure; in the medical field, for monitoring blood pressure, blood flow, and respiratory pressure; in industrial applications, for measuring hydraulic and gas pressures; and in the aerospace sector, they are crucial for flight safety, measuring altitude, speed, and other pressure parameters. As technology continues to advance and innovate, ceramic pressure sensors will continue to expand their application fields, meet increasingly demanding requirements, and play an increasingly important role.
Post time: Mar-04-2024