Imagine this: It’s a cold winter morning, and you’re about to start your daily commute. As you jump into your car and start the engine, an unwelcome beep breaks the silence: the annoying low tire pressure warning. You check the tires, but everything seems fine. What’s going on?
In most cases, it’s not a real issue with your tire pressure. The culprit behind this false alarm is the interaction between temperature and the tire pressure sensor. As the temperature drops, the air inside the tires contracts, causing a slight decrease in pressure. However, under normal conditions, this pressure drop might not be enough to trigger the alarm system.
But like any electronic component, tire pressure sensors can be affected by temperature fluctuations. In cold environments, the sensor’s sensitivity and accuracy may decrease, leading it to mistakenly interpret minor pressure changes as significant drops, triggering a frustrating false alarm.
This phenomenon highlights the importance of pressure sensor stability. A stable sensor will maintain its accuracy and sensitivity over a wide temperature range, ensuring reliable tire pressure readings even in harsh winter conditions.
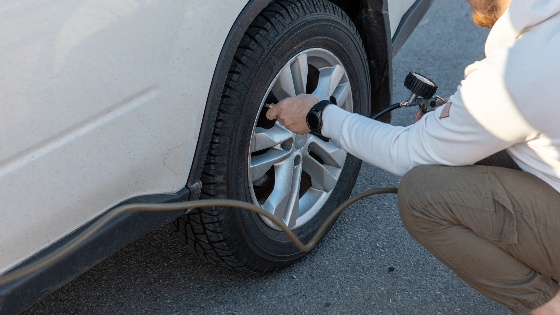
What is Pressure Sensor Stability?
According to ISO 17034:2016, pressure sensor stability is a crucial parameter for ensuring the accurate and reliable operation of pressure measurement systems. It refers to the sensor’s ability to maintain its performance characteristics over a period of time when faced with environmental and operational challenges. This period is typically one year. Stability affects the sensor’s accuracy, repeatability, and overall lifespan, making it vital in applications ranging from industrial automation to medical devices.
Long-term Stability, Short-term Stability, Repeatability
Long-term Stability Long-term stability refers to the sensor’s ability to maintain its accuracy and consistency over extended periods. For example, a sensor with a long-term stability of 0.01% full scale per year may only drift by 1.5 Pa over a 15-year usage period. This means the sensor’s readings remain reliable even after long-term use.
Short-term Stability Short-term stability involves the sensor’s performance consistency over shorter periods (e.g., hours or days). Short-term stability is crucial for applications requiring rapid and precise measurements. The sensor’s short-term performance reflects its design and manufacturing quality.
Repeatability Repeatability refers to the consistency of the sensor’s readings when measured multiple times under the same conditions. A highly repeatable sensor should show very close results in each measurement, ensuring the reliability and precision of the measurement process. Good repeatability means the sensor can provide consistent results under various operational conditions.
Zero Drift and Sensitivity Drift
- Zero Drift: Zero drift refers to changes in the sensor output when no pressure is applied. Zero drift can cause the measurement baseline to shift, affecting accuracy. This drift may result from environmental changes or long-term use.
- Sensitivity Drift: Sensitivity drift refers to changes in the sensor’s output capability when the same pressure is applied. Sensitivity drift affects the sensor’s response to pressure changes, leading to measurement deviations.
Temperature Stability
Temperature stability refers to the sensor’s performance changes under different temperature environments. Temperature changes can cause the sensor materials to expand or contract, affecting its output. Good temperature stability means the sensor can maintain consistent measurement performance over a wide temperature range, which is crucial for sensors operating in extreme temperature environments.
Factors Affecting Pressure Sensor Stability
- Environmental Factors: Exposure to temperature, humidity, and contaminants can cause sensor drift and reduce accuracy. Extreme temperature changes can cause sensor materials to expand or contract, excessive humidity can corrode or short-circuit sensor components, and contaminants can clog the sensor’s sensitive elements, affecting normal operation.
- Mechanical Stress: Vibration, shock, and mechanical stress during installation can affect the sensor’s structural integrity. Long-term vibration can loosen or damage internal components, severe shock can directly damage the sensor, and improper installation can deform or misalign the sensor, affecting accuracy and stability.
- Aging: Materials and components age over time, affecting stability. Sensor materials may experience fatigue, wear, or performance degradation after long-term use. This aging effect can reduce sensor sensitivity, slow response speed, and increase error, affecting long-term stability and reliability.
- Temperature Changes: Temperature changes cause sensor materials to expand and contract, requiring effective temperature compensation techniques. Sensor performance may vary at different temperatures, such as zero drift and sensitivity changes. Effective temperature compensation techniques, such as using reference sensors, correction algorithms, and selecting low thermal expansion coefficient materials, are necessary to ensure the sensor maintains high accuracy and stability under various temperature conditions.
XIDIBEI adopts various measures to ensure pressure sensor stability, including:
- High-Quality Material Selection XIDIBEI selects high-quality materials such as stainless steel, silicon, and ceramics. These materials have high strength, thermal stability, and resistance to environmental factors, ensuring durability and stability in extreme conditions.
- Advanced Manufacturing Technology XIDIBEI utilizes advanced manufacturing processes, such as Micro-Electro-Mechanical Systems (MEMS) technology, to improve product accuracy and reliability. MEMS technology enables high sensitivity and precision in compact structures.
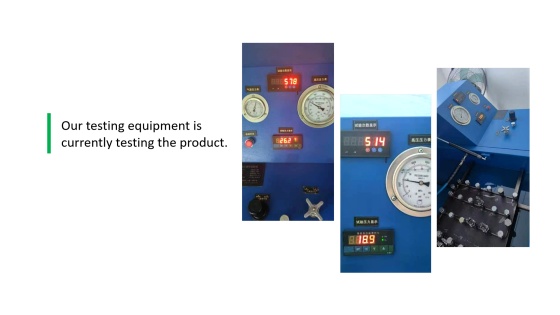
- Rigorous Testing and Calibration Each sensor undergoes rigorous environmental testing and calibration before leaving the factory. The testing process includes temperature cycling, pressure cycling, and long-term stability tests to ensure high performance under extreme conditions. For example, heat treatment technology is used for artificial aging to simulate long-term stability in use.
- Innovative Compensation Techniques XIDIBEI has developed advanced temperature and mechanical stress compensation techniques. Temperature compensation ensures stable output under different temperature conditions using reference sensors and correction algorithms. Mechanical stress compensation reduces performance changes caused by vibration and shock through optimized sensor design and installation methods.
- Regular Maintenance and Calibration XIDIBEI recommends regular calibration and maintenance of sensors. Regular calibration can correct sensor drift caused by environmental changes and long-term use, ensuring continuous accurate readings.
Application Cases
XIDIBEI’s pressure sensors are widely used in industrial process control, automotive system monitoring, medical device monitoring, and aerospace. In these applications, sensor stability and reliability are crucial. For example, in the automotive industry, XIDIBEI sensors monitor engine and tire pressure, ensuring optimal vehicle performance and safety; in medical devices, they monitor vital signs, ensuring normal operation and patient safety.
Summary
By using high-quality materials, advanced manufacturing technology, rigorous testing and calibration, innovative compensation techniques, and regular maintenance and calibration, XIDIBEI ensures long-term stability and reliability of its pressure sensors in various extreme environments. XIDIBEI continues to commit to technological innovation, providing customers with more stable and reliable pressure sensor solutions.
Post time: Jun-05-2024