Introduction
In the field of modern sensing technology, piezoresistive pressure sensors stand out for their precision, reliability, and versatility. These sensors utilize the piezoresistive effect to measure pressure changes and play a pivotal role in a wide range of applications from industrial automation to medical monitoring. This article delves into the fundamentals of piezoresistive pressure sensors, including their principles, types, applications, advantages, and considerations for use.
Understanding Piezoresistive Pressure Sensors
The Principle of Piezoresistance
The piezoresistive effect is a physical phenomenon where the electrical resistance of a material changes due to mechanical stress. This effect is widely applied in various sensors, such as pressure sensors, accelerometers, force sensors, and torque sensors, which work by converting physical quantities into electrical signals. They leverage the high sensitivity, wide measurement range, quick frequency response, and the advantages of simple structure and relatively low cost of the piezoresistive effect.
Components and Materials
Piezoresistive pressure sensors primarily operate through their core component, a sensitive membrane or diaphragm made from materials like single-crystal silicon, polysilicon, or metal films. When the membrane deforms under pressure, the resulting mechanical stress changes its electrical resistance, converting pressure changes into electrical signals. The choice of material and the design of the membrane, including its shape, thickness, and structure, significantly impact the sensor's sensitivity, measurement range, temperature characteristics, linearity, and stability.
Single-crystal silicon is widely used for its high piezoresistive coefficient and sensitivity, despite its strong temperature sensitivity; polysilicon and metal films are chosen for their weaker temperature sensitivity or good stability and corrosion resistance. Optimizing performance also relies on the design of the Wheatstone bridge circuit and the application of compensation technologies, such as temperature compensation and zero-point calibration, to reduce the impact of temperature variations and zero-point drift, thus enhancing the accuracy and stability of measurements.
Types of Piezoresistive Sensors
Piezoresistive pressure sensors are categorized into absolute, gauge, and differential types based on their measurement approach. Absolute pressure sensors are used to measure pressure relative to a perfect vacuum, suitable for vacuum systems and meteorological measurements, known for their sealed chamber structure and wide measurement range. Gauge pressure sensors measure pressure relative to atmospheric pressure, applicable in hydraulic and pneumatic systems, characterized by their simple structure and low cost. Differential pressure sensors measure the difference between two pressure sources, widely used in flow and level measurements, and noted for their high precision but more complex structure.
Selecting the appropriate piezoresistive pressure sensor involves considering the application scenario and measurement needs, where absolute sensors offer high precision but at a higher cost, gauge sensors are low-cost but with limited measurement range, and differential sensors are unaffected by atmospheric pressure but come at a higher cost. Additionally, the market offers specialized sensors designed for specific needs, such as miniature pressure sensors, high-temperature pressure sensors, and corrosion-resistant pressure sensors, each targeting different measurement environments and conditions.

The Working Principle of Piezoresistive Pressure Sensors
The Science Behind Piezoresistance
Piezoresistive pressure sensors work based on the piezoresistive effect, where the electrical resistance of a material changes under mechanical stress. When pressure is applied to a sensitive membrane or diaphragm, causing it to deform and generate mechanical stress, this stress alters the membrane's electrical resistance. The sensor then converts this resistance change into an electrical signal through a Wheatstone bridge circuit, which, after amplification and filtering, is transformed into a readable pressure value. This process involves changes in the material's crystal structure, where mechanical stress affects electron mobility and carrier concentration, leading to a change in resistance.
Several factors influence the performance of piezoresistive pressure sensors, including the piezoresistive material's coefficient, temperature coefficient, stability, the membrane's shape, thickness, structure, and the design of the Wheatstone bridge circuit and the application of compensation technologies such as temperature compensation and zero-point calibration. The piezoresistive coefficient is a critical parameter indicating the strength of the material's piezoresistive effect, while the Wheatstone bridge is an essential circuit for precisely converting resistance changes into voltage signals, improving the accuracy and stability of measurements.
Applications of Piezoresistive Pressure Sensors
Piezoresistive pressure sensors are extensively used in various fields such as industrial control, medical instruments, automotive electronics, and aerospace due to their high sensitivity, wide measurement range, quick frequency response, simple structure, and relative low cost. These sensors monitor pressure in hydraulic and pneumatic systems in the manufacturing industry, measure torque and pressure in robotic joints, and ensure the safety and efficiency of production processes in the petrochemical, power, and metallurgical industries.
In the medical field, piezoresistive pressure sensors are used to monitor critical parameters like blood pressure, blood flow, and respiratory pressure, providing crucial technical support for diagnosing ventricular pressure, intracranial pressure, and eye pressure. They also play roles in wearable health technologies by monitoring physical activity and sleep quality. In the automotive industry, these sensors measure tire pressure, engine pressure, and fuel pressure, while in aerospace, they support the accurate measurement of flight altitude, airspeed, and engine pressure.
Beyond these areas, piezoresistive pressure sensors also play an important role in environmental monitoring and scientific research, measuring atmospheric pressure, water levels, and wind speed, and providing precise data for material mechanics and fluid dynamics studies. The diverse applications of these sensors highlight their key position in modern technology and industrial development, making them an indispensable technology for efficient, precise monitoring and control.
Advantages of Piezoresistive Pressure Sensors
Piezoresistive pressure sensors, with their high sensitivity and accuracy, multifunctionality and wide measurement range, simple structure, and low cost, play an indispensable role in various fields. These sensors can detect extremely small pressure changes, making them suitable for high-precision measurement applications, such as monitoring blood pressure and blood flow in medical monitoring. They can also be designed to meet the needs of different pressure ranges from micro pascals to megapascals, demonstrating their wide applicability in industrial control systems, automotive electronics, aerospace, and other areas.
The manufacturing process of piezoresistive pressure sensors is simple and relatively inexpensive, combined with their compact size, quick frequency response, long-term stability, and strong anti-interference capability, making them easy to maintain and replace, while suitable for dynamic measurement and complex environmental pressure monitoring. These characteristics not only reduce the overall operational costs but also ensure the efficient and reliable operation of the system.
Limitations and Considerations
While piezoresistive pressure sensors are widely used in various industries due to their high sensitivity, wide measurement range, simple structure, and cost-effectiveness, their use also comes with a series of limitations that need to be considered in practical applications. Environmental factors such as temperature, humidity, and vibration significantly affect sensor performance, potentially leading to sensitivity changes, zero-point drift, and decreased measurement accuracy. Additionally, the high sensitivity of piezoresistive sensors, although enabling them to detect minute pressure changes, also makes them more susceptible to noise interference.
To address these challenges, adopting appropriate temperature compensation measures, vibration prevention strategies, and regular calibration can significantly improve the measurement accuracy and stability of sensors. Although piezoresistive pressure sensors have certain limitations in measurement range and media compatibility, selecting the appropriate sensor type and model and designing sensors for specific application environments can effectively mitigate these limitations. Moreover, while high-precision piezoresistive pressure sensors are relatively expensive, investing in the right sensors and adopting corresponding optimization measures can enhance the overall performance and reliability of the system in the long run.
In summary, despite some limitations, piezoresistive pressure sensors can maximize their advantages and meet the needs of various complex applications through rational selection and precise application design. This requires users to fully consider key parameters such as environmental factors, measurement range, and media compatibility during selection and use, and to adopt corresponding measures to ensure the accuracy and stability of sensors.
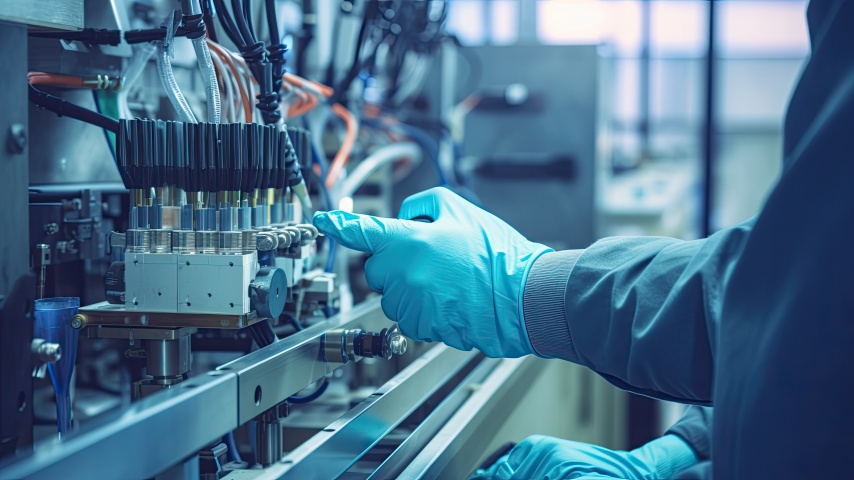
Innovations in Piezoresistive Pressure Sensing Technology
Advancements in Materials and Technology
The continuous progress in material science and technology is revolutionizing the development of piezoresistive pressure sensors, mainly reflected in the development of new piezoresistive materials, the application of microfabrication technology, the integration of compensation and wireless technologies, and the incorporation of intelligent technologies. New piezoresistive materials such as nanomaterials and semiconductor materials not only provide higher piezoresistive coefficients and lower temperature coefficients but also enhance sensor stability, significantly improving sensor sensitivity and accuracy.
The application of microfabrication technology enables the production of miniature, high-precision pressure sensors, reducing costs and increasing production efficiency, allowing sensors to be deployed in a wider range of application scenarios. Furthermore, advanced compensation technologies like temperature compensation and zero-point drift compensation further enhance the accuracy and stability of measurements. The integration of wireless technology also makes data transmission more convenient, greatly enhancing the flexibility of installation and use and improving system safety.
The Future Direction of Pressure Sensing Technology
Intelligent technologies, combining sensing technology, microelectronics technology, and computer technology, are driving piezoresistive pressure sensors toward more intelligent development. This not only realizes intelligent measurement, data analysis, and fault diagnosis functions but also significantly enhances the efficiency and value of sensors in practical applications. For example, the application of nanomaterials greatly improves sensitivity and measurement range, MEMS technology realizes sensor miniaturization and cost reduction, digital signal processing technology significantly enhances measurement accuracy and stability, and wireless sensing technology provides the possibility of wireless data transmission for sensors. These advancements collectively promote the rapid development and expansion of applications for piezoresistive pressure sensor technology.
Selecting the Appropriate Piezoresistive Pressure Sensor
Selection Criteria
When selecting a piezoresistive pressure sensor, key factors such as measurement range, sensitivity, and environmental conditions are crucial. Ensuring that the selected sensor's measurement range covers the required pressure range is essential to avoid exceeding its performance limits and causing measurement errors. Sensitivity is another decisive factor, directly affecting measurement accuracy; thus, choosing a sensor with appropriate sensitivity for the application's accuracy requirements is necessary. Additionally, environmental factors such as temperature, humidity, and vibration can also impact sensor performance, making it essential to select sensors that can adapt to specific application environmental conditions.
Selecting a piezoresistive pressure sensor suitable for a specific application also requires considering other factors such as size, weight, and cost. For instance, industrial control applications typically need sensors with a wide measurement range, high sensitivity, and strong anti-interference capability, while medical instruments prioritize high measurement accuracy, good stability, and excellent biocompatibility. Sensors for the automotive electronics field need to be compact, lightweight, withstand high temperatures, and be vibration-resistant, whereas sensors for the aerospace field require extremely high measurement accuracy, stability, and radiation resistance. Therefore, understanding and evaluating each application's specific needs and selecting the most suitable piezoresistive pressure sensor model is critical for ensuring optimal system performance and long-term reliability.
Post time: Mar-12-2024