Imagine you're driving and enjoying the scenery when suddenly, a heavy downpour turns into a torrential rainstorm. Despite the windshield wipers working at full speed, visibility continues to decrease. You pull over, hoping the storm will soon pass.
As you wait, you can't help but marvel at the durability of your car. It has withstood countless weather conditions, from scorching heat to cold, and still performs excellently. What makes it so resilient?
The answer lies in a process called thick-film technology. This innovative technology creates electronic circuits that can endure harsh environments by layering conductive and resistive materials on a substrate.
Thick-film components are like tiny warriors, protecting their environment. They can withstand extreme temperatures, high humidity, and even physical shocks and vibrations, making them widely used in demanding fields such as automotive, aerospace, and industrial applications.
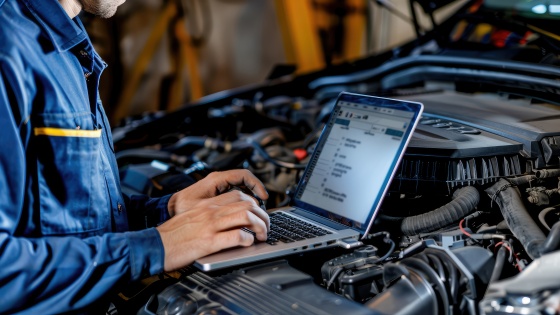
Introduction to Thick Film Technology
Definition and Overview
Thick film technology is a process used in the manufacturing of electronic circuits. It involves depositing layers of materials onto a substrate, such as ceramic, glass, or metal, to form electronic components. The thickness of these layers typically ranges from 10 to 100 micrometers. Compared to thin film technology, thick film technology has thicker material layers, providing higher mechanical strength and durability.
Basic Definition
Thick film technology involves depositing conductive, insulating, and resistive materials onto a substrate using methods like screen printing and spraying. These materials are then sintered at high temperatures to ensure strong adhesion. The sintering process usually occurs at temperatures between 850°C and 950°C, ensuring good adhesion and stability of the material layers.
Historical Development
Origin and Evolution
Thick film technology originated in the early 20th century with the rapid development of the electronics industry, driven by the need for high-performance and reliable electronic components. It was first applied in the radio and television industries, where early devices required precise and reliable electronic components. Engineers developed methods to deposit thick layers of materials onto substrates to form electronic circuits, marking the beginning of thick film technology.
In the 1950s, thick film technology began to be used in industrial applications, primarily for manufacturing resistors and simple electronic circuits. With the development of the semiconductor industry in the 1960s and 1970s, thick film technology was increasingly used in more complex circuit manufacturing. During this period, high-temperature sintering processes were introduced to enhance material adhesion and stability, expanding the application of thick film processes in electronic manufacturing.
By the 1980s, thick film technology had further developed and gained popularity, especially in the manufacturing of hybrid circuits and multilayer circuit boards. During this time, the variety of materials and applications for thick film processes expanded significantly. From the 1990s to the present, thick film technology has been widely used in the production of sensors, medical devices, automotive electronics, and power electronics. Modern thick film technology continues to improve, incorporating advanced materials and processes to further solidify its role in electronic manufacturing.
Importance and Applications
Key Application Areas and Significance of Thick Film Technology
Thick film technology holds a crucial position in modern electronic manufacturing due to its broad application areas and significant importance. Firstly, thick film technology is widely used in electronic circuit manufacturing, particularly in the production of printed circuit boards (PCBs) and hybrid circuits. Its excellent conductive properties and thermal stability make thick film circuits ideal for high-frequency and high-power applications.
Secondly, thick film technology plays a vital role in sensor manufacturing. Various types of sensors, such as pressure sensors, temperature sensors, and gas sensors, rely on thick film technology for high precision and reliability. For instance, thick film pressure sensors convert pressure changes into electrical signals by depositing resistive materials onto a substrate.
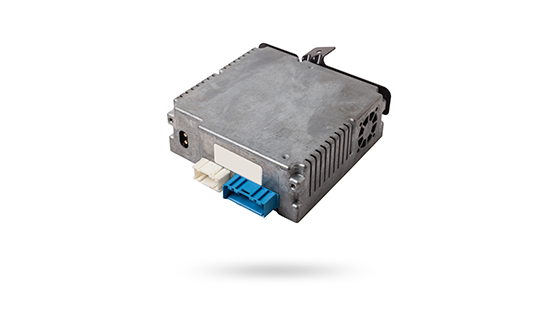
Additionally, thick film technology is extensively applied in automotive electronics, medical devices, and power electronic devices. In automotive electronics, thick film technology is used to manufacture key components like engine control units (ECUs), anti-lock braking systems (ABS), and airbag control systems, known for their high-temperature resistance and vibration durability. In medical devices, thick film technology is used to produce electrocardiographs, ultrasound equipment, and blood glucose monitors, where high reliability and accuracy are critical.
Overall, thick film technology plays an irreplaceable role in modern electronic manufacturing due to its high reliability, precision, and versatility. Its applications in multiple key fields not only enhance product performance and quality but also drive continuous technological advancement and innovation.
Materials Used in Thick Film Technology
1. Conductive Materials
Common conductive materials used in thick film technology include gold, silver, platinum, palladium, and copper. These materials are widely used due to their excellent conductivity and corrosion resistance. For example, gold and silver, known for their high conductivity, are suitable for high-frequency and high-power circuits. Platinum and palladium, with their good chemical stability, are often used in high-temperature and corrosion-resistant circuits. Although copper is cost-effective, it oxidizes easily, requiring surface treatment to enhance its durability.
2. Resistive and Dielectric Materials
Resistive and dielectric materials are also crucial in thick film technology. Common resistive materials include ruthenium oxide (RuO₂) and ruthenium-titanium oxide (RuTiO₂), which provide stable and precise resistance values and are widely used in precision resistor manufacturing. Dielectric materials, typically glass or ceramic, such as alumina (Al₂O₃) and barium titanate (BaTiO₃), offer excellent insulation properties and dielectric constants, used in capacitor and isolation layer manufacturing to ensure electrical insulation and stability of circuits.
3. Substrate Materials
Substrate materials commonly used in thick film circuits include ceramic, glass, and metal. Ceramic substrates like alumina (Al₂O₃) and aluminum nitride (AlN) are favored for their excellent thermal conductivity and mechanical strength, widely used in high-power and high-frequency circuits. Glass substrates, known for their good insulation and processing properties, are often used in low-power and multilayer circuit manufacturing. Metal substrates like copper and aluminum, with their excellent thermal conductivity, are used in circuits requiring high heat dissipation.
Thick Film Printing Processes
1. Screen Printing
Screen printing is a method of transferring ink onto a substrate through a screen. In thick film technology, screen printing deposits conductive, insulating, and resistive materials onto substrates. The process involves controlling the material deposition area through patterns on the screen. The advantages of screen printing include ease of operation, low cost, and adaptability, suitable for printing on various substrates and mass production.
2. Photolithography
Photolithography is a high-precision printing process that transfers patterns onto substrates using photosensitive materials and masks. The process involves coating with photosensitive material, exposure, development, and etching. The advantages of photolithography include achieving high-resolution and fine patterns, suitable for manufacturing complex circuits. However, the complexity and high cost of photolithography equipment and processes make it less suitable for large-scale production.
Sintering
1. Temperature Profile
Sintering is a critical step in thick film technology, where high temperatures ensure that printed material layers adhere to the substrate. Proper temperature control during sintering is crucial, typically involving three stages: heating, holding, and cooling. Proper temperature control ensures material adhesion and stability, avoiding cracks and peeling.
2. Equipment and Techniques
Sintering equipment includes box furnaces, belt furnaces, and laser sintering equipment. Box furnaces are suitable for small-scale production, allowing precise control of temperature and atmosphere. Belt furnaces are ideal for large-scale production with high efficiency and continuous operation. Laser sintering equipment uses laser beams for localized heating, suitable for high-precision and localized sintering applications.
3. Impact on Material Properties
The sintering process significantly affects material properties. Proper sintering can enhance mechanical strength, conductivity, and durability. Excessive or insufficient sintering temperatures can degrade material properties, causing over-sintering and deformation or incomplete sintering, affecting adhesion and electrical properties.
Applications of Thick Film Technology
Applications in the Sensor Field
Thick film technology is crucial in sensor manufacturing, used in various sensors, including pressure sensors, temperature sensors, gas sensors, and humidity sensors. Its excellent electrical performance, mechanical strength, and environmental adaptability make thick film sensors widely applicable in industrial, automotive, medical, and consumer electronics.
For example, XIDIBEI's XDB305 and XDB306T series pressure sensors utilize this technology. By combining ceramic substrates and thick film resistor networks and using high-temperature sintering, resistive materials firmly bond to the substrate, achieving high-precision and high-reliability pressure measurement. These sensors are widely used in automotive engine control, industrial process control, and medical equipment, providing stable pressure measurement and feedback.
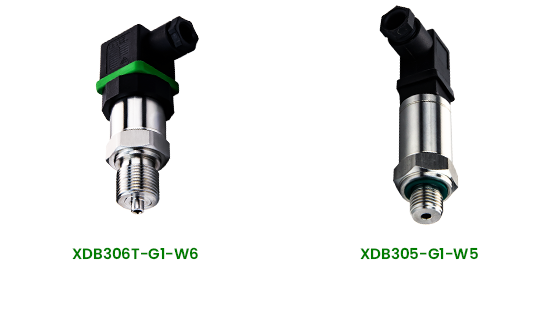
Thick film temperature sensors detect temperature changes through the temperature coefficient of thick film resistive materials. These sensors feature fast response, high accuracy, and high-temperature resistance, suitable for various high-temperature environments. For instance, in automotive electronic systems, thick film temperature sensors monitor engine and exhaust system temperatures, ensuring vehicle safety. In industrial automation, these sensors monitor equipment temperature changes, preventing overheating and damage.
Thick film technology is also extensively used in gas sensors and humidity sensors. Thick film gas sensors utilize specific materials' sensitivity to gases, forming highly sensitive and selective sensors through thick film technology. These sensors are widely used in environmental monitoring, industrial safety, and home air quality control. Thick film humidity sensors detect humidity changes using thick film resistive or capacitive materials, widely used in meteorological observation, agricultural environment monitoring, and smart homes.
Continuous innovation and improvement in thick film technology will continue to play a vital role in the sensor field, meeting the demand for high-performance sensors across various industries.
Applications in Other Fields
1. Electronics and Semiconductor Industry
Thick film technology is widely used in the electronics and semiconductor industry. Its excellent conductivity and thermal stability make it ideal for manufacturing printed circuit boards (PCBs), hybrid circuits, and multilayer circuit boards. In high-frequency and high-power circuits, thick film technology provides reliable electrical performance and mechanical strength, suitable for various electronic devices and semiconductor modules. Additionally, thick film technology is used to manufacture resistors, capacitors, and inductive components, essential parts of electronic circuits.
2. Medical Devices
Thick film technology is extremely important in medical devices, providing high precision and reliability for various critical medical electronics. For example, thick film sensors are widely used in blood pressure monitors, electrocardiographs, and ultrasound equipment, offering precise measurement and diagnostic data. Additionally, thick film circuits are used in wearable medical devices and implantable electronic devices, ensuring stable operation inside and outside the body. The corrosion resistance and biocompatibility of thick film technology further enhance its value in medical applications.
3. Automotive Industry
Thick film technology is widely used in various automotive electronic control systems. Key components like automotive electronic control units (ECUs), anti-lock braking systems (ABS), and airbag control systems rely on thick film technology for high-temperature resistance and vibration durability. Thick film resistors and sensors play crucial roles in engine management, body control, and safety systems, ensuring vehicle operation under various conditions. Additionally, thick film technology is used in manufacturing high-performance electronic components in automotive lighting and audio systems.
4. Renewable Energy
Thick film technology is increasingly applied in renewable energy systems. Its excellent conductivity and thermal stability make it a crucial component of solar cells, wind energy conversion systems, and energy storage devices. In solar cells, thick film technology is used to manufacture efficient conductive layers and electrodes, enhancing photoelectric conversion efficiency. In wind energy conversion systems and energy storage devices, thick film circuits and sensors achieve high-precision energy monitoring and management, improving system efficiency and reliability.
Advantages of Thick Film Technology
1. High Reliability and Durability
Thick film circuits are widely favored for their high reliability and durability. Thick film technology ensures excellent mechanical strength and electrical performance by sintering conductive, insulating, and resistive materials onto substrates. These circuits can operate stably in harsh environments, resistant to high temperatures, humidity, and corrosion, making them suitable for high-reliability applications such as automotive electronics, industrial control, and medical devices.
2. Cost-Effectiveness
Thick film technology offers significant cost advantages. Compared to other high-precision manufacturing processes, thick film technology has lower material and process costs. Screen printing and high-temperature sintering processes are relatively simple, with lower equipment investment and maintenance costs. Additionally, thick film technology is suitable for mass production, with high production efficiency, further reducing per-unit production costs.
3. Customization and Flexibility
Thick film technology provides a high degree of customization and flexibility. Different electrical and mechanical properties can be achieved by adjusting screen printing patterns and material formulations. Thick film technology can print on various substrates, meeting diverse application needs. This flexibility allows thick film technology to meet specific customer requirements, gaining a competitive advantage in the market.
Challenges of Thick Film Technology
1. Environmental Issues
Thick film technology faces some environmental challenges in production and application. For example, the high temperatures and waste gases generated during sintering may cause environmental pollution. Additionally, some thick film materials contain heavy metals and other harmful substances, requiring special environmental protection measures during manufacturing and disposal to minimize environmental impact.
2. Technical Limitations
Thick film technology has some technical limitations. The pattern precision of thick film circuits is relatively low due to the resolution limitations of screen printing, making it unsuitable for ultra-high precision and miniaturized circuit manufacturing. Additionally, the choice of materials and control of the sintering process directly impact circuit performance, requiring careful balancing and optimization during design and manufacturing.
3. Market Competition
Thick film technology faces market competition from other advanced manufacturing technologies. Thin film technology and printed electronics offer higher precision and smaller sizes in some applications, gradually encroaching on thick film technology's market share. To maintain an advantage in the competitive market, thick film technology must continuously innovate and improve to enhance its performance and application scope.
Innovation in Thick Film Technology
1. Nanomaterials
Nanomaterials have significantly improved performance in thick film technology. Nanoparticles have larger surface areas and better physical and chemical properties, significantly enhancing the conductivity, sensitivity, and reliability of thick film circuits. For example, using nanomaterials like nano-silver and nano-gold in thick film circuits achieves higher conductivity and finer patterns, meeting the needs of high-performance electronic devices.
2. Advanced Printing Technologies
Advanced printing technologies, such as inkjet printing and laser direct writing, bring new possibilities to thick film technology. These technologies achieve higher resolution and finer patterns, helping improve circuit precision and integration. Additionally, advanced printing technologies reduce material waste and production costs, increasing production efficiency.
3. Integration with Other Technologies
Combining thick film technology with other technologies is a crucial direction for future development. For example, integrating thick film technology with flexible electronics enables the manufacturing of flexible and wearable electronic devices. Thick film technology can also combine with microelectromechanical systems (MEMS) technology to produce high-precision and high-sensitivity sensors and actuators. These integrated applications will further expand the application fields and market space of thick film technology.
Future Trends of Thick Film Technology
1. Growth in IoT Applications
The rapid development of the Internet of Things (IoT) brings new growth opportunities for thick film technology. With the surge in IoT devices, the demand for high-precision, high-reliability, and low-cost sensors increases significantly. Thick film technology, with its excellent performance and flexible applications, meets the sensor needs of IoT devices. For example, thick film sensors play a crucial role in IoT applications such as smart homes, industrial automation, and environmental monitoring. The development of thick film technology will further promote the miniaturization and intelligence of IoT devices.
2. Advancements in Material Science
Advancements in material science provide new momentum for the development of thick film technology. Developing new conductive materials, semiconductor materials, and insulating materials continually improves the performance of thick film circuits. For example, the introduction of nanomaterials significantly enhances the conductivity and sensitivity of thick film circuits. Additionally, the application of flexible substrates and transparent conductive materials enables the widespread use of thick film technology in flexible electronics and transparent electronic devices. These advancements in material science will unlock the enormous potential of thick film technology in emerging applications.
3. Emerging Market Opportunities
Thick film technology has broad application prospects in emerging markets such as wearable technology and smart textiles. Wearable devices like smartwatches, health monitors, and fitness trackers require lightweight, durable, and high-performance electronic components, which thick film technology can provide. Additionally, smart textiles integrate electronic components into fabrics, achieving health monitoring, environmental sensing, and interactive functions, where thick film technology has significant advantages. As these emerging markets continue to expand, thick film technology will experience new development opportunities.
Post time: Jun-13-2024