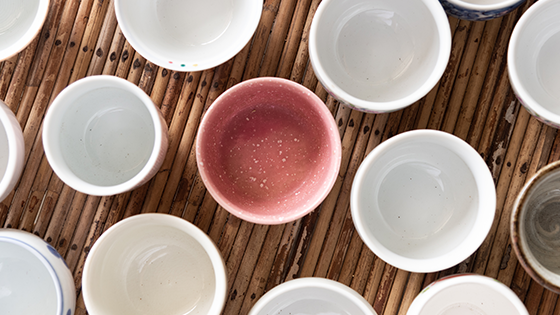
Introduction
In our daily lives, we frequently encounter ceramic products like porcelain bowls, vases, and ceramic cups. These ceramics are not only aesthetically pleasing but also highly practical. Their durability and corrosion resistance make them popular among consumers. However, the application of ceramic materials extends far beyond household items. In modern industry, ceramics are valued for their unique physical and chemical properties, making them essential in many high-tech fields.
Industrial ceramics stand out for their significant advantages, particularly in manufacturing pressure sensors. Ceramic materials maintain stable performance in extreme environments and offer high durability and reliability, making them an ideal choice for pressure sensor production.
In the following sections, we will explore the advantages of using ceramic materials in pressure sensors. First, we will introduce the properties of ceramics, including their high-temperature resistance, corrosion resistance, mechanical strength, and electrical insulation. Next, we will analyze the specific benefits of ceramic pressure sensors and provide examples of their applications in various fields. Finally, we will discuss the development trends of ceramic pressure sensors, focusing on new materials and technologies.
Properties of Ceramic Materials
The application of ceramic materials in pressure sensors is attributed to a series of superior properties. Firstly, ceramics exhibit excellent high-temperature resistance. For example, ceramic tableware used in microwaves or ovens can maintain their physical properties under high temperatures. Similarly, industrial ceramics can function stably in extreme temperatures, making them suitable for high-temperature applications.
Secondly, ceramic materials are highly resistant to corrosion. Ceramic vases do not rust or corrode when holding flowers and water, demonstrating their excellent performance in chemical environments. Industrial ceramics can withstand acidic and alkaline environments for extended periods without damage due to their outstanding corrosion resistance.
Additionally, ceramic materials possess high mechanical strength. Although ceramic bowls used daily may break easily, industrial ceramics, after special treatment, become very hard and wear-resistant. This makes them suitable for high-pressure and high-stress environments, ensuring they remain intact and functional under harsh conditions.
Finally, ceramics are excellent electrical insulators. Everyday ceramic insulators effectively showcase this property. In industrial applications, ceramic materials prevent electrical leakage, ensuring the safe operation of sensors under high pressure and protecting the sensors and related equipment.
These properties make ceramic materials crucial in the manufacturing of pressure sensors. In the following sections, we will further explore the specific advantages of ceramic pressure sensors and their applications in various fields.
Advantages of Ceramic Pressure Sensors
Ceramic pressure sensors stand out in numerous applications due to their exceptional performance. Firstly, ceramic sensors are renowned for their high precision and long-term stability, making them suitable for precise measurements. Whether in laboratory settings or industrial production, ceramic sensors provide accurate and reliable data, assisting engineers and scientists in making accurate analyses and decisions.
Moreover, the durability of ceramic materials endows these sensors with a long lifespan and robustness. The sturdy and wear-resistant nature of ceramics ensures that sensors are not easily damaged during use, reducing maintenance costs and replacement frequency, and thus enhancing overall equipment efficiency.
Another significant advantage of ceramic sensors is their excellent environmental resistance. Whether in high-temperature, high-humidity, or corrosive environments, ceramic sensors can function normally. This makes them particularly suitable for extreme conditions such as petrochemical, marine exploration, and aerospace fields, ensuring stable performance in harsh environments.
Finally, ceramic sensors possess superior linearity and sensitivity. This means they maintain consistent linear relationships when responding to pressure changes, ensuring measurement accuracy and reliability. High sensitivity enables sensors to detect even slight pressure changes, suitable for high-precision measurement applications like medical devices and precision instruments.
These advantages make ceramic pressure sensors widely used across various industries and the preferred choice for many demanding applications. In the following sections, we will discuss the specific application areas of ceramic pressure sensors and how they add value to different industries.
Application Areas of Ceramic Pressure Sensors
Ceramic pressure sensors, with their outstanding performance and durability, are widely used in numerous industries.
In the automotive industry, ceramic pressure sensors are extensively used for pressure measurement in engine management, braking systems, and fuel injection systems. Engine management systems require precise pressure data to optimize fuel mixture and ignition timing, ensuring efficient engine operation. In braking systems, pressure sensors help monitor and control brake fluid pressure, ensuring vehicle safety. In fuel injection systems, sensors measure fuel pressure, ensuring the engine receives the appropriate amount of fuel.
In the aerospace sector, ceramic pressure sensors are used for pressure monitoring in aircraft pneumatic and hydraulic systems. Aircraft require precise pressure data under various flight conditions to maintain stable flight attitudes and control. Pressure sensors in hydraulic systems help ensure the proper functioning of hydraulic circuits, preventing system failures.
In medical devices, ceramic pressure sensors are employed for precise pressure detection in equipment such as blood pressure monitors and ventilators. Pressure sensors in blood pressure monitors provide accurate pressure readings, aiding doctors in diagnosing and monitoring patients' blood pressure. In ventilators, pressure sensors help control gas flow and pressure, ensuring patients receive adequate respiratory support.
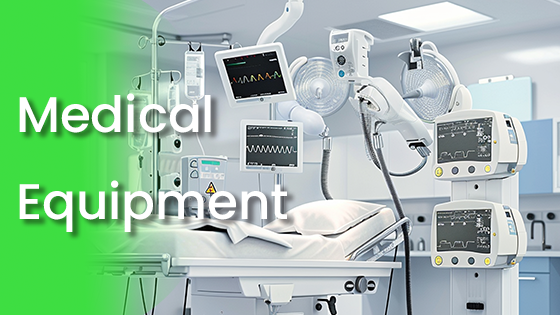
In industrial automation, ceramic pressure sensors are used for pressure control and monitoring in hydraulic and pneumatic systems. Pressure sensors in hydraulic systems help control hydraulic pressure, ensuring the normal operation and efficiency of mechanical equipment. In pneumatic systems, pressure sensors monitor gas pressure, maintaining system stability and safety.
In water treatment and environmental protection, ceramic pressure sensors are used for pressure sensing in sewage treatment and environmental monitoring. During sewage treatment, sensors monitor pressure in pipes and containers, helping control and optimize treatment processes. In environmental monitoring, pressure sensors detect pressure changes in water bodies and the atmosphere, providing environmental data to support environmental protection decisions.
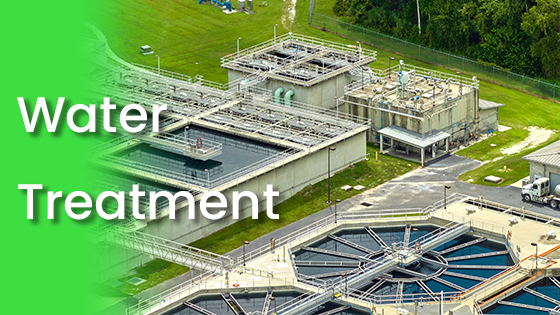
These application areas demonstrate the importance and versatility of ceramic pressure sensors in various scenarios. Next, we will explore the development trends of ceramic pressure sensors, discussing the application prospects of new materials and technologies.
Product Introduction
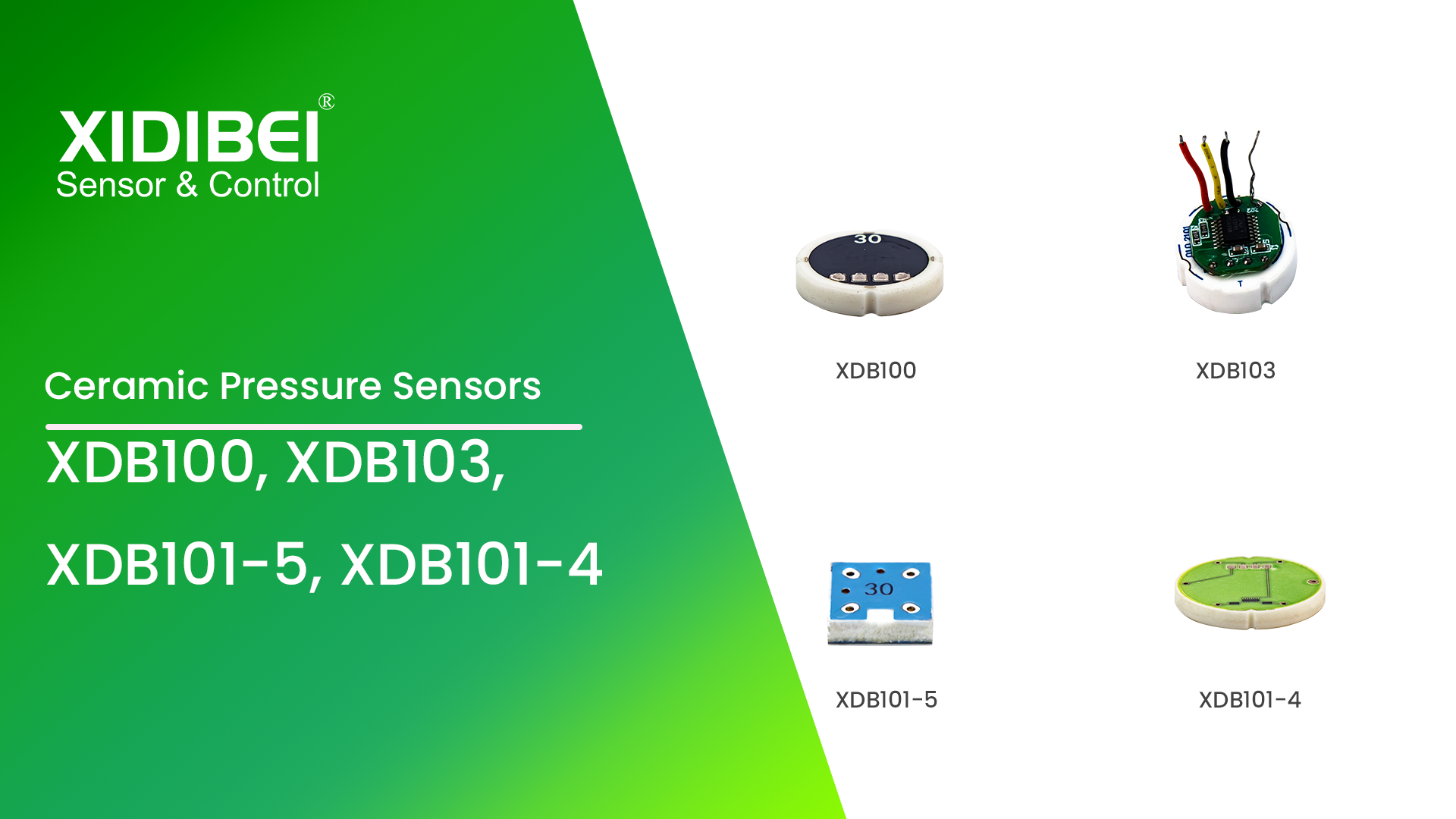
This section will detail the advantages and applications of four ceramic pressure sensor products from XIDIBEI.
XDB100 Piezoresistive Monolithic Ceramic Pressure Sensor:
High Precision and Stability: The XDB100 offers extremely high precision and long-term stability, providing accurate pressure measurement results.
High Temperature and Corrosion Resistance: This sensor functions stably in high-temperature and corrosive environments, making it suitable for demanding industrial applications.
Application Example: Widely used in the automotive industry for engine management and braking systems, ensuring vehicle safety and reliability.
XDB103 Ceramic Pressure Sensor Module:
Excellent Environmental Resistance: The XDB103 has outstanding resistance to high temperatures, high humidity, and corrosion, allowing it to function normally in extreme environments.
Modular Design: Its modular design makes it easy to integrate into various systems, enhancing installation and maintenance convenience.
Application Example: Used in the aerospace sector for pressure monitoring in aircraft pneumatic and hydraulic systems, ensuring flight safety.
XDB101-5 Square Flush Diaphragm Ceramic Pressure Sensor:
Precision Pressure Detection: The XDB101-5 provides high-precision pressure detection, suitable for applications requiring precise pressure measurement.
High Durability: Made of high-strength ceramic material, this sensor boasts excellent durability and a long lifespan.
Application Example: In medical devices like blood pressure monitors and ventilators, the XDB101-5 ensures accurate pressure detection for safe and precise medical operations.
XDB101-4 Micro Pressure Flush Diaphragm Ceramic Pressure Sensor:
High Sensitivity and Linearity: The XDB101-4 features high sensitivity and excellent linearity, capable of detecting minor pressure changes.
Compact Design: Its small size meets the miniaturization needs of modern equipment.
Application Example: In industrial automation, the XDB101-4 is used for pressure control and monitoring in hydraulic and pneumatic systems, achieving efficient and precise automation.

Development Trends of Ceramic Pressure Sensors
The development of ceramic pressure sensors is marked by several key trends. First, the application of new materials and technologies is driving advancements in this field. For example, the development and use of nanoceramics and composite materials offer new possibilities for enhancing sensor performance. These new materials can improve sensor sensitivity and precision while also enhancing durability and environmental adaptability.
Second, miniaturization and integration are crucial development directions. As modern equipment increasingly demands compact and energy-efficient designs, smaller and smarter sensor designs are becoming more important. Miniaturization allows sensors to be more easily integrated into various complex systems, meeting diverse application needs.
Additionally, the combination of intelligence and the Internet of Things (IoT) represents a significant future trend. Integrating ceramic pressure sensors with IoT technology enables remote monitoring and data analysis, enhancing system intelligence. For instance, sensors can transmit real-time data to the cloud, where big data analysis and artificial intelligence techniques can be applied for predictive maintenance and optimized operations, improving efficiency and reliability.
Conclusion
In summary, the application of ceramic materials in pressure sensors demonstrates unique advantages, including high-temperature resistance, corrosion resistance, high mechanical strength, and excellent electrical insulation. XIDIBEI's four ceramic pressure sensors—XDB100, XDB103, XDB101-5, and XDB101-4—exhibit exceptional performance and reliability across the automotive, aerospace, medical, industrial automation, and environmental protection sectors. These products enhance technological levels in various fields and lay a solid foundation for future innovation.
Looking ahead, with the continuous emergence of new materials and technologies and the development of miniaturization, integration, and intelligence, ceramic pressure sensors will play a more significant role in more applications. We anticipate these sensors to offer higher precision, better stability, and more intelligent features, bringing more innovation and value to various industries.
Post time: Jul-24-2024